Tested quality ensures performance for cameras & components
Our customers' trust is closely linked to our high quality standards: every product we manufacture is extensively tested. We also thoroughly inspect purchased vision accessories and check their compatibility. After all, the perfect interaction of all components is the basis for the optimum performance of vision systems.
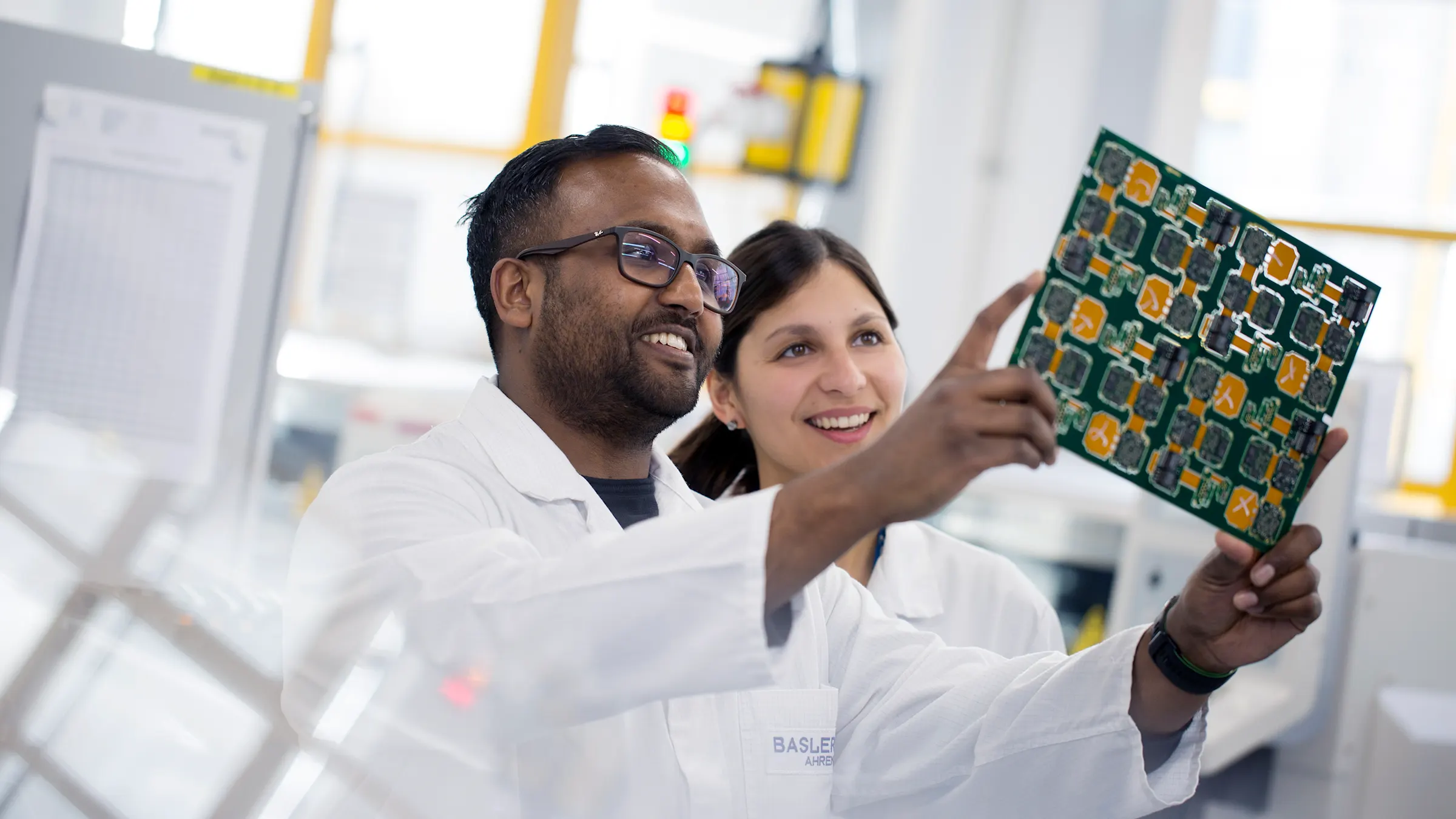
9 + 1 tests in quality assurance
Before we ship a camera, we conduct 9+1 quality tests. “9” stands for standard tests, “1” for your customized test.Only 0.1% failure rate in camera production
This low failure rate in the first 6 months after delivery for self-produced cameras demonstrates the high quality of our products.All components from a single source
Basler offers all vision system components from a single source. Lower integration costs and a shortened time-to-market save time and money.Continuously high quality
Continuous optimization helps us reduce waste, make production more efficient and solve problems in the long term.
Quality assurance
We attach great importance to the highest quality and reliability of our products. To ensure that our cameras deliver what we promise in your application, they undergo extensive testing.
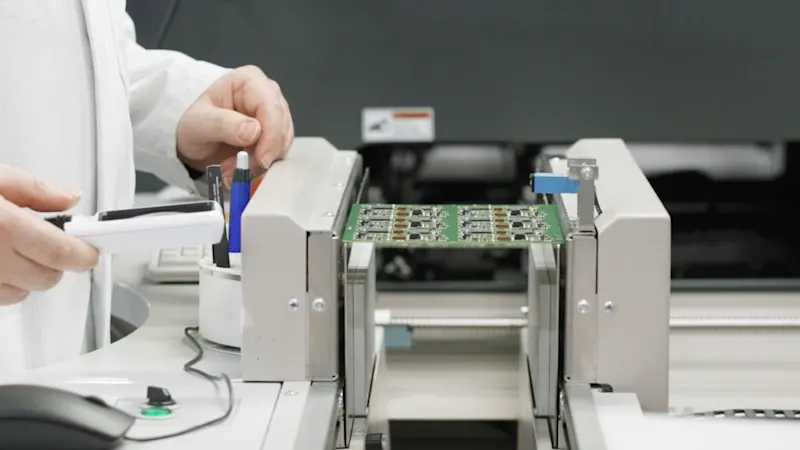
Seamless monitoring
We rely on seamless monitoring to ensure high quality in production. For example, standardized quality assurance processes for all of our camera models that we use in our production. This enables us to reliably guarantee consistently high quality. Every camera we produce undergoes 9 + 1 tests.
Suppliers of accessory products are also subject to stringent requirements: Our development department intensively checks all supplier products, including regular function and interoperability tests. Particular attention is always paid to the compatibility of all components with Basler cameras.
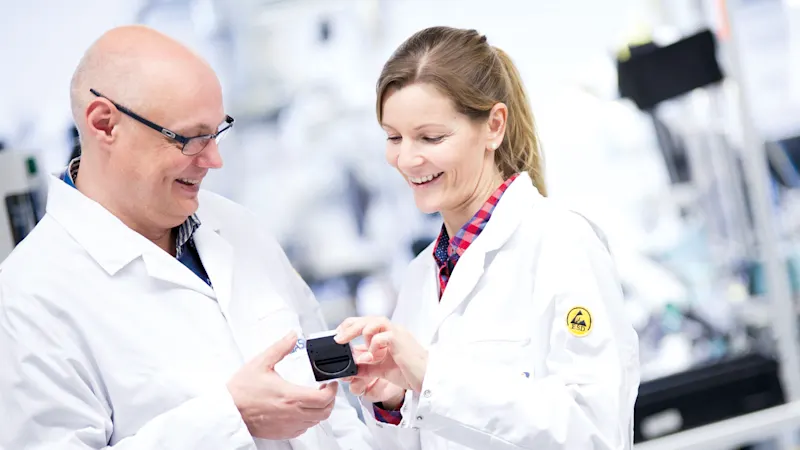
Better quality management and standardization
We take various quality measures in the production and procurement of our Vision products. To this end, we rely on lean, efficient production to reduce effort, errors and therefore costs. This enables us to offer you high-quality cameras and other vision components - at a reliable price-performance ratio.
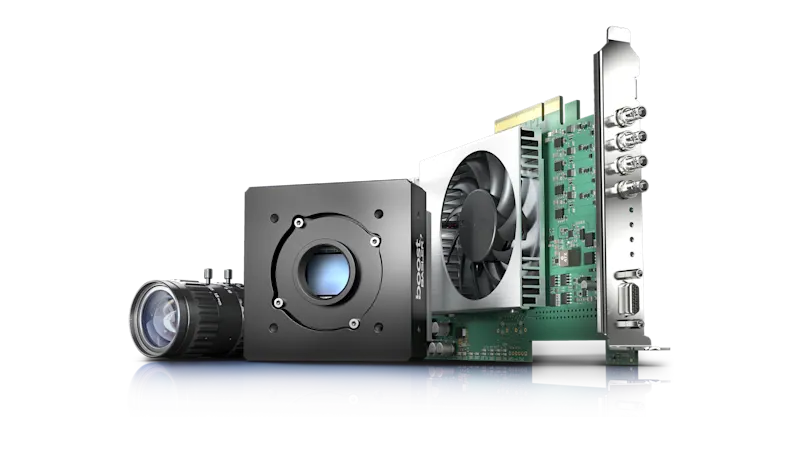
3-year warranty
Our customers receive a three-year warranty on all Basler products. Basler stands for high reliability, even beyond the camera: In addition to the Basler camera portfolio, the three-year warranty also applies to the entire Basler accessories portfolio—including Basler frame grabbers, lenses, and cables. For 3rd party products, the warranty of the respective manufacturer applies.
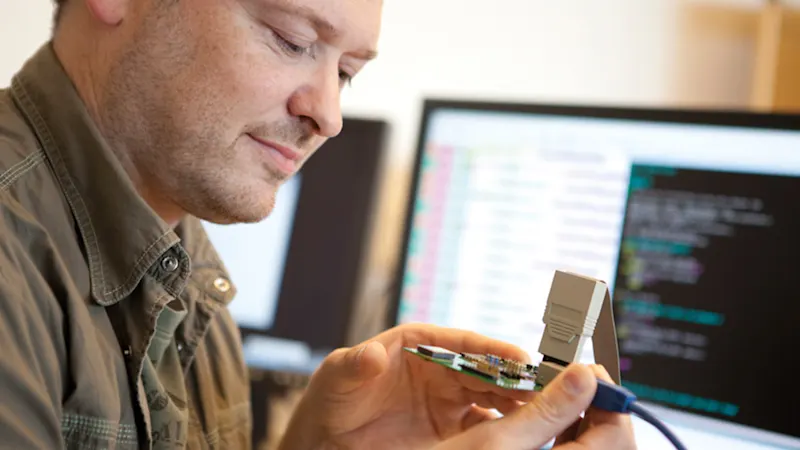
Well-trained employees
Continuous improvement processes help us to keep moving forward: We invest a lot in the further development of our employees. Their creativity and knowledge helps the company to improve processes and reduce waste. As a result, production can be made ever more efficient.
Regular meetings as part of our store floor management make production processes more transparent for managers and therefore easier to understand. This also allows progress in key figures to be evaluated and the need for improvement to be prioritized accordingly.
Compatibility
To ensure optimum functionality in various applications, we ensure smooth interaction between all components and a simple system setup.
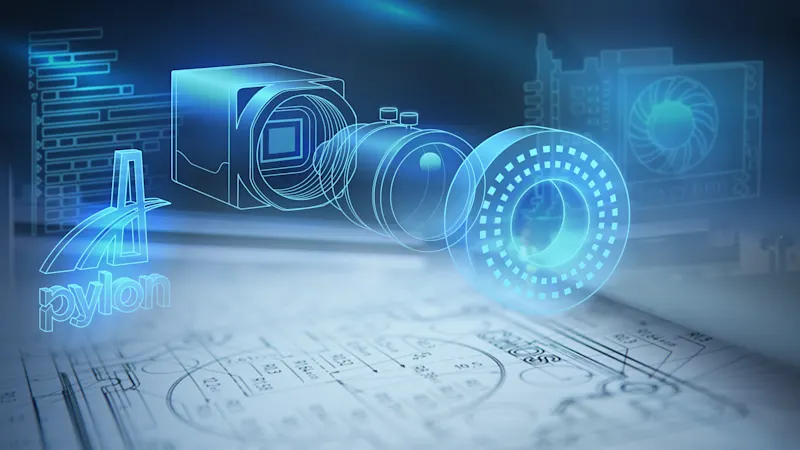
Lean Design
Right from the product development stage, we focus on the essentials: customer benefits. With Lean Product Design , we concentrate on technical approaches that really deliver benefits and reduce system complexity. In all process steps, we pursue the goal of avoiding anything superfluous. We prefer to focus on clear functionality that is easy to understand.
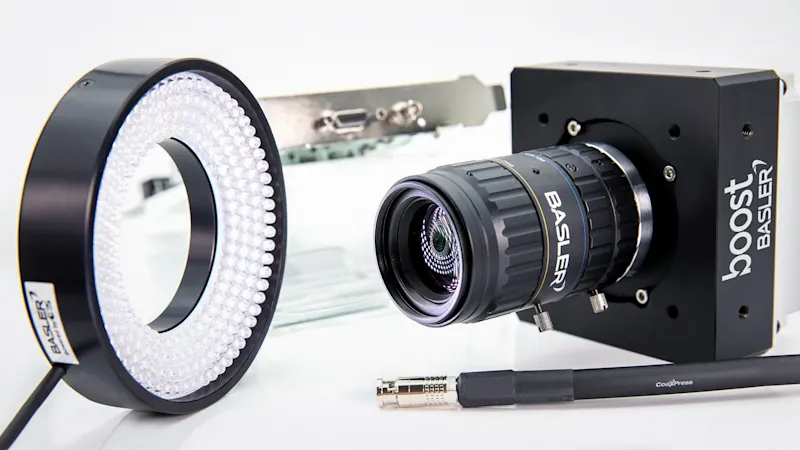
Interoperability
Only a lens, a light source, reliable data transmission and other components together with the camera make up a vision system. The key to the high quality and reliability of a vision solution lies in the compatibility and interoperability of all components. When designing, specifying and selecting components that we do not manufacture ourselves, our engineers pay particular attention to the exact interaction of all components.
Standards
We rely on standards for easy integration and comparability of our products.
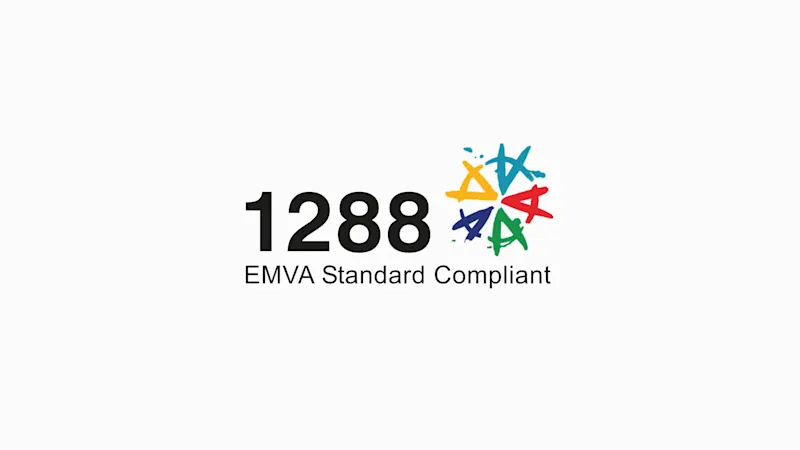
EMVA standard
EMVA Standard Camera Characterization is the final measure we take to ensure the consistent utility of our cameras once they leave our facility. By testing our cameras against European Machine Vision Association (EMVA) is an association of companies and corporations involved in machine vision and standardization in that field.">EMVA standard 1288 (which covers such performance characteristics as spectral sensitivity, color and signal-to-noise ratio) and including comparative performance data on our data sheets, Basler simplifies the camera selection process for you and ensures you’ll get the performance you need from your system.
To the EMVA standard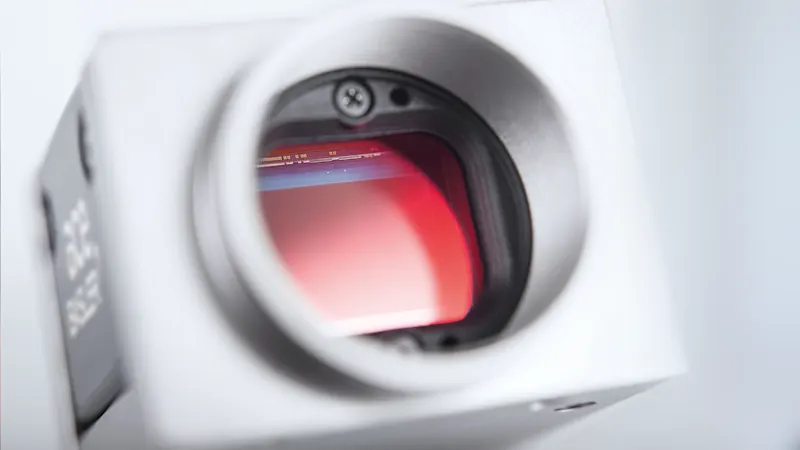
Compliance
We attach great importance to the highest quality and reliability of our products. All legal requirements and standards must be met 100%.
To the overview of all conformities