Quality Assurance
Test procedures at Basler
Delivering products with the highest quality and reliability is of great importance to us. To ensure that our cameras deliver our promised performance for your application, they undergo extensive testing.
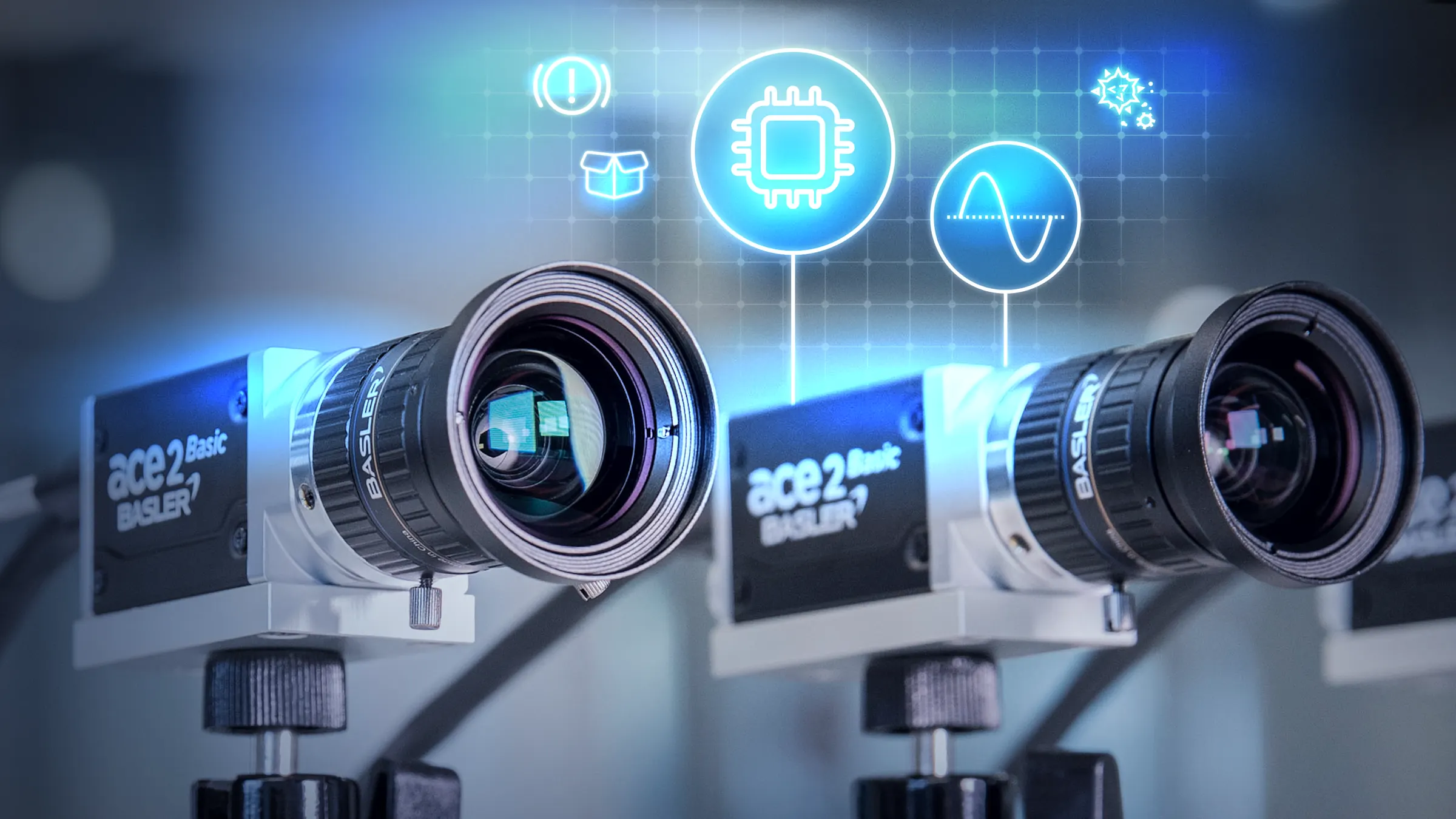
9 + 1 tests in production
"9 + 1" stands for nine standard tests plus one additional customer-specific test that our cameras will undergo during production, including tests in board and camera production. We rely on seamless monitoring to ensure our products are of the highest quality before they are shipped to you.
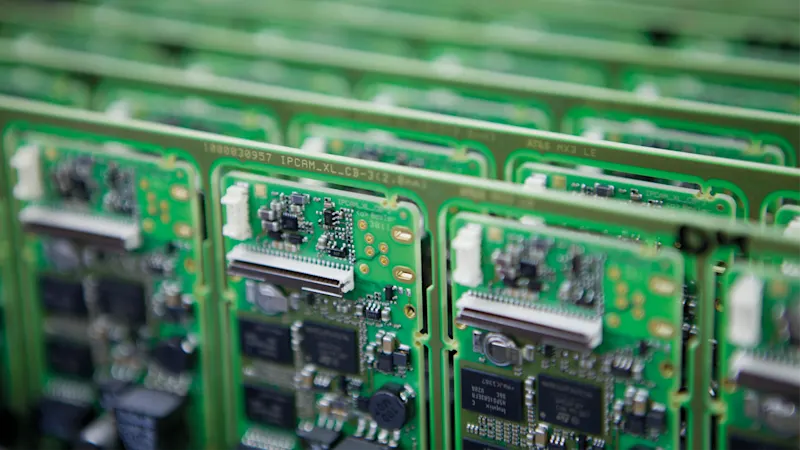
Quality in board production
During board production, we rely on statistical process control. Both components and boards go through a series of tests:
Incoming goods control to eliminate externally defective components
Paste inspection to ensure highly robust solder joints
Automatic optical inspection of the boards according to IPC-A-610
X-ray solder joint inspection for BGA's to check hidden solder joints
Electrical board test to ensure boards are functioning properly. If a board does not pass this test, an error analysis is performed by the "board doctor".
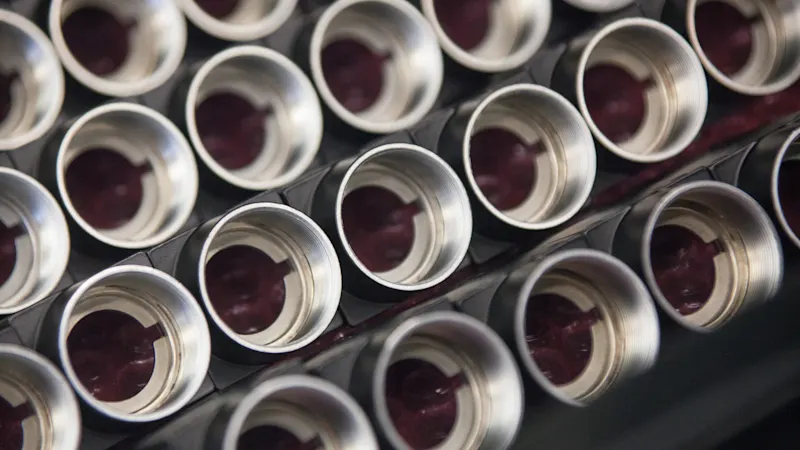
Quality in camera production
All camera production takes place under clean room conditions (ISO 14644 class 8) in several steps. We therefore perform several quality tests:
Sensor cleaning to prevent dust and other particles in the optical path from causing image artifacts
Sensor alignment to ensure the sensor and mount are parallel
Our proprietary camera test tool (CTT) runs an automated test, loads the firmware, calibrates the camera, and checks it according to EMVA standard 1288. This CTT test is adapted for each camera platform.
Shipping test to ensure that all quality tests have been successfully passed before the product is labeled and shipped
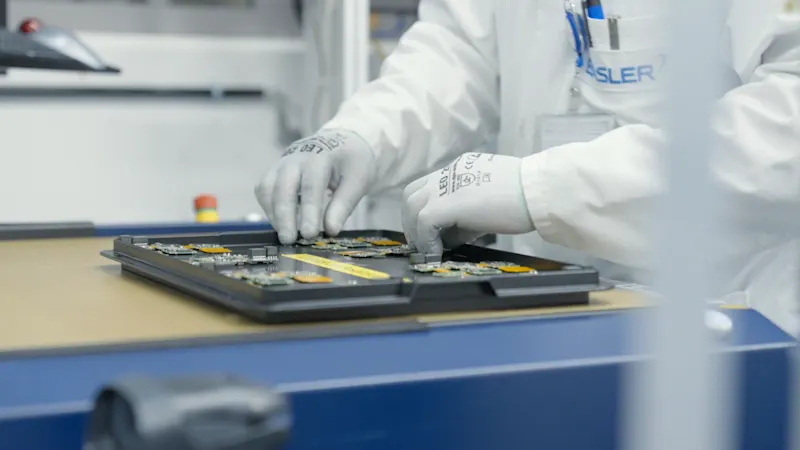
Quality assurance for components
Our responsible development department intensively checks all supplier products, e.g. with regular function and interoperability tests. The compatibility of all components with Basler cameras is checked particularly carefully.
Regular supplier audits also ensure a consistently high level of quality. By providing all necessary certifications, the seamless quality assurance of all vision products offered by Basler is transparently documented for our customers.
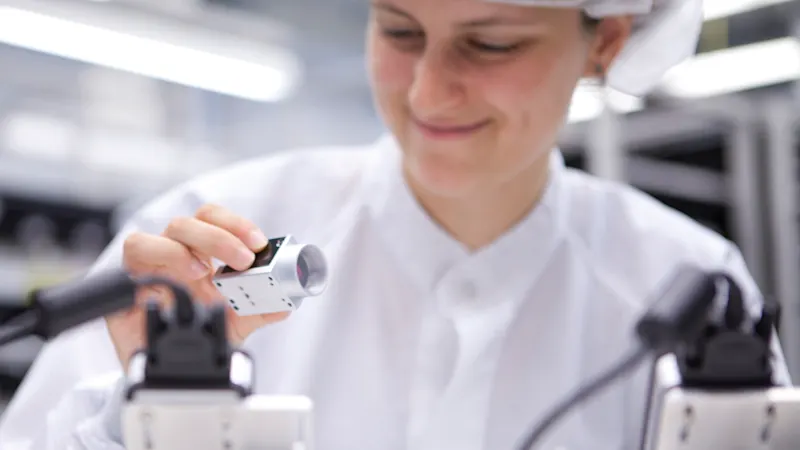
Customer-specific quality tests
On request, we supplement our standard tests with customer-specific tests. For example, if you need a camera with a fixed, preset lens, we will adjust the lens, bond the camera and lens, and then test the lens settings.
Sequence of the 9 standard quality tests during board and camera production
Quality assurance starts even earlier: test procedures in development
In additional to quality assurance tests during the production of our cameras, we also investigate possible use cases during the development process that may affect the lifetime of the camera or its operation.
External factors, such as
the ambient temperature and any temperature fluctuations,
existing moisture in and around the application area, and
the number and amplitude of temperature cycles related to switching on/off
can influence the lifetime of a camera.
Internal factors, such as
the robustness of individual electronic components,
the robustness of conductor paths and solder joints, and
the design of the camera's cooling mechanism.
To ensure that none of these factors affect the performance and lifetime of your camera, Basler has developed special test procedures for new camera development projects. They effectively map these internal and external factors, allowing us to design cameras protected from their influence. For example, a test of representative temperature cycles was developed, which are simulated in a climate chamber.