How Does Basler Make Its Cameras So Robust?
Highest quality requirements and extensive tests ensure high robustness
Long before they are ever boxed for shipping to customers, all Basler cameras are subjected to a comprehensive and demanding program of testing. We inspect every component and carefully weigh its use before it lands inside a Basler camera. Our quality assurance measures already start during development and ensure a particularly high robustness of our cameras.
Quality is more than just a promise at Basler
We place highest demands on our products and take numerous measures to provide you with the quality and robustness you expect from us. Our standard internal quality assurance processes start when components are delivered to Basler's production facilities. All components and modules are subject to multiple inspection steps before and after placement on the circuit boards. They must pass each step before they are released for assembly into the camera. These inspection processes continue seamlessly in production. The general functional check, the image quality check using the camera test tool and the check of the sensor position within the camera are just three further inspection steps that a Basler camera must satisfy during production.
Test factors taken into account
In addition to these steps in the production of the cameras, we are also investigating possible influences during the development process that affect a camera’s lifespan, especially if the camera is exposed to them in various ways for the duration of its lifespan.
External factors can include
the ambient temperature with its possible fluctuations
moisture levels in the area of application, and
the number and amplitude of temperature cycles related to switch-on/off.
These can impact the lifespan of a camera, as can
internal factors, such as
the robustness of individual electronic components,
the robustness of PCBT and solder joints and
the design of the camera's heat-dissipation mechanism.
Special test procedures
To ensure that none of these factors interfere with the performance and lifespan of your camera, Basler has developed special test procedures for new camera developments, designed to capture these influences and protect the cameras effectively against them. For example, representative temperature cycles were developed as test, which are simulated in a climate cabinet.
You can find out more about quality management and assurance in production at Basler on our quality pages or in our quality brochure.
Case Study: Temperature Test of Components
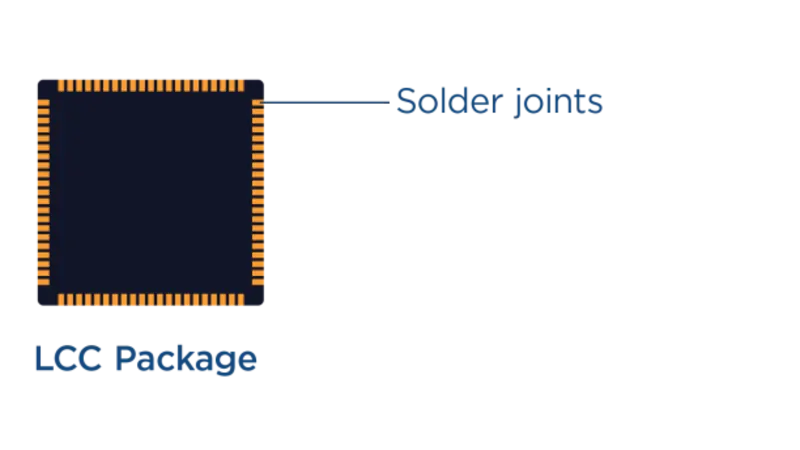
This graphic shows the setup of the sensor package of the PYTHON 2000 and PYTHON 5000 sensors from ON Semiconductor.
When temperatures fluctuate, the ceramic housing of the sensor expands less than the board beneath it. When subjected to repeated test cycles, it was shown that the so-called LCC package's solder joints along the outer edge of the sensor package are, when arranged as shown in the graphic above, not robust enough to reliably survive the stress created by the different expansion/contraction cycles.
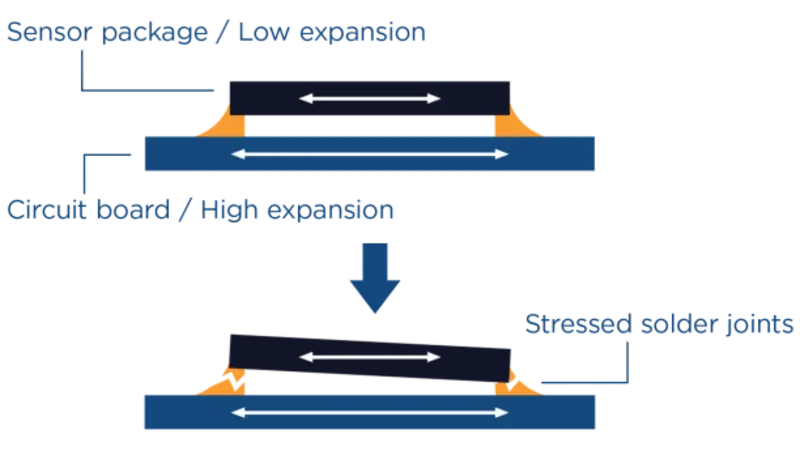
A package of this kind can lead to camera models being used only for selected applications where the number and amplitude of the temperature cycles are very low, otherwise the high stress causes soldering joints to break in the medium to long term and thus the functionality of the Sensor is limited or suspended.
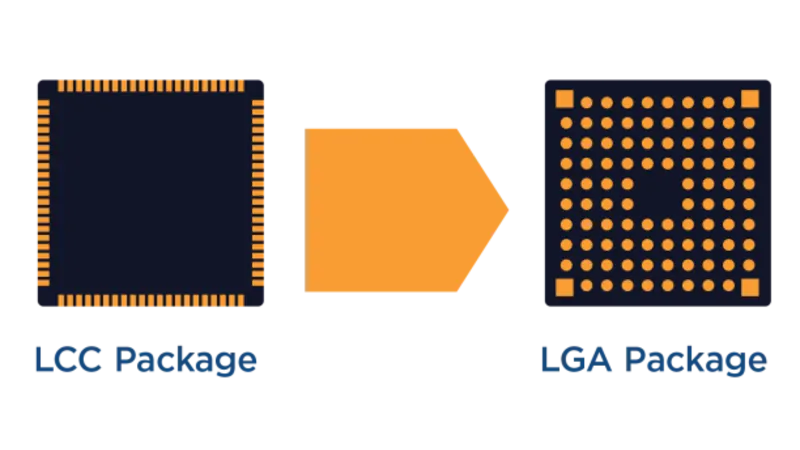
These limited possibilities of use in customer applications only partially fulfill Basler's high quality standards for its cameras. Basler engineers sought after potential alternatives. Working with the sensor manufacturer, they established the following solution:
In contrast to the LCC package, the newly developed LGA sensor package features multiple solder joints spread around the entire surface. As such, it is demonstrably more resistant to expansion related to temperature fluctuations ― thus fulfilling Basler's high quality demands.
What Quality Means at Basler
Our video on the case study explores the individual steps involved in developing the new LGA sensor package: