Quality control of aluminum cans
Inline inspection after the wash cycle
Following the washing process, beverage cans are conveyed on a wide, high-throughput line exposed to splashing water and water vapor. An IP67-rated vision system ensures reliable operation in these demanding conditions. When paired with polarization filters, reflective glare is minimized, enabling high-contrast image acquisition for accurate analysis by the AI software. This setup supports robust, real-time inspection and maximizes process stability.
Large quantities, intensive washing process and highly reflective surfaces
The IP67 Vision products provide a robust solution for inline inspection following the wash cycle. Their high ingress protection rating and broad product portfolio make them well-suited for this demanding process step. The offering includes area scan cameras, industrial lenses, protective lens housings, and IP67-rated lighting—ensuring reliable performance in wet and high-throughput environments.
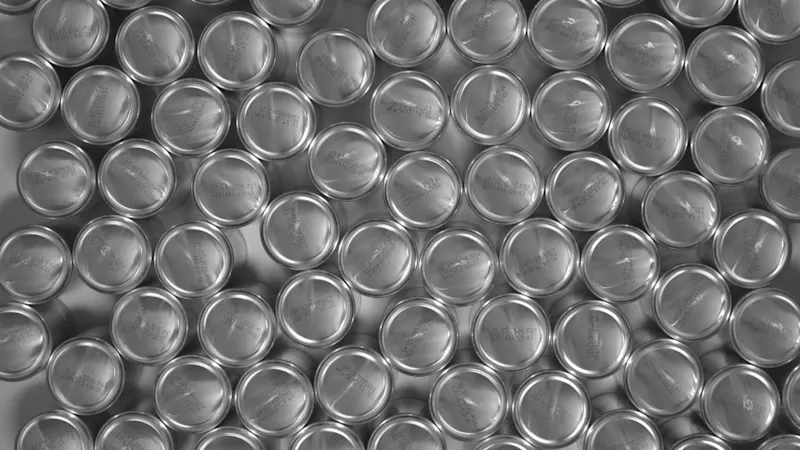
2,000 cans per minute
After washing, the cans are moved on a mass conveyor belt with a width of 3 m. Depending on the type of system, can size and line configuration, modern production lines achieve
1,200 to 2,000 cans per minute.
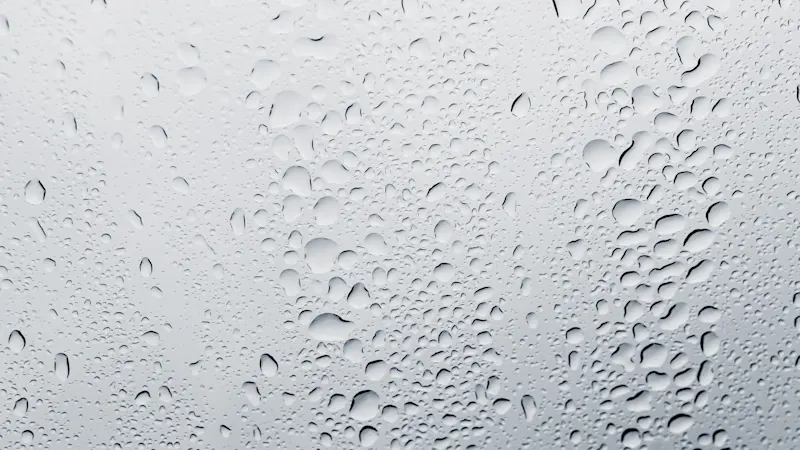
Hot water and cleaner
Rinsing with hot water and alkaline cleaners removes residues such as lubricants and metal particles. This creates humid air, spray water and vapors or aerosols containing cleaning agents. These require IP67 protection for the sensitive electronic components of vision systems.
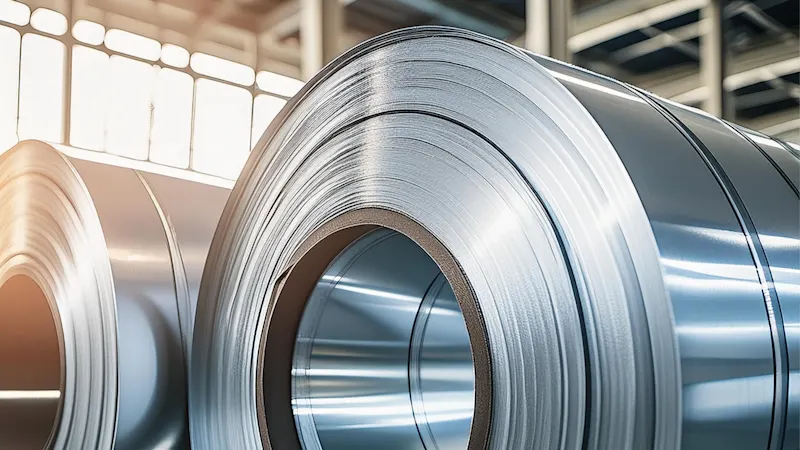
Aluminum
The smooth surface of the aluminum strongly reflects incident light rays. Thesereflections create bright spots in the image. Optimizing lighting and camera settings minimizes these reflections, ensuring reliable and precise image analysis.
What are the actual environmental conditions in your application? The protection of the vision system depends on the details: if aggressive chemicals such as acids or alkalis are used, a project-specific adaptation of our products is a sensible option.
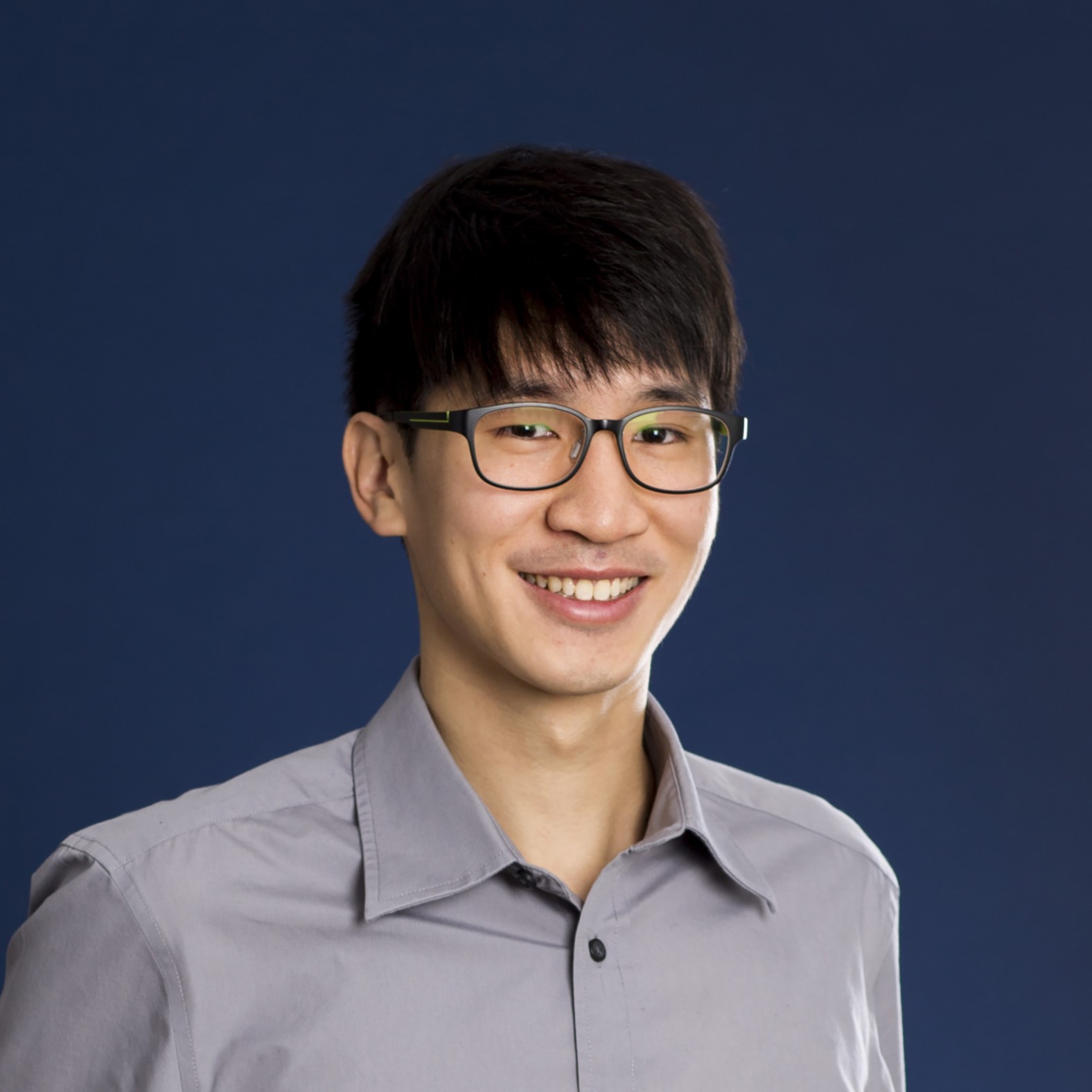
The right system setup for the right image quality
Speed, working distance and field of view: good image quality is required for precise and robust AI decisions to be made in the next step. With a suitable area scan camera, protected lens and other IP67 components, the camera system can also be used in difficult environmental conditions.
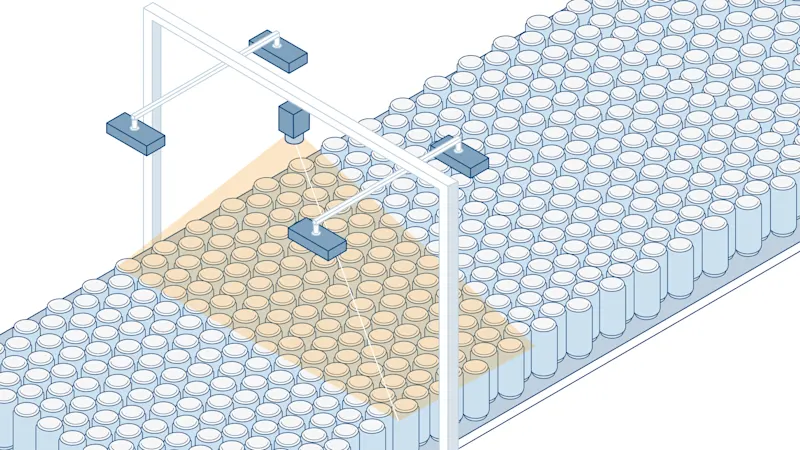
Vision system with bar lighting for wide conveyor belts
For the inspection on conveyor belts of up to 3 m width, we rely on an optimized system design with a working distance of approx. 1.8 m. We use the ace 2 a2A5320-7gmIP67 camera with the high-resolution IMX542 sensor and an f8.5 mm lens, which provides a 3 m wide field of view with low distortion. The resulting resolution of 0.6 mm/pixel enables a detailed evaluation across the entire width of the conveyor belt.
At 2,000 cans per minute, the maximum exposure time is around 15 ms before motion blur occurs. Higher throughput requires correspondingly shorter exposure times.
The system is complemented by four IP67-protected bar lights, which are mounted in line.
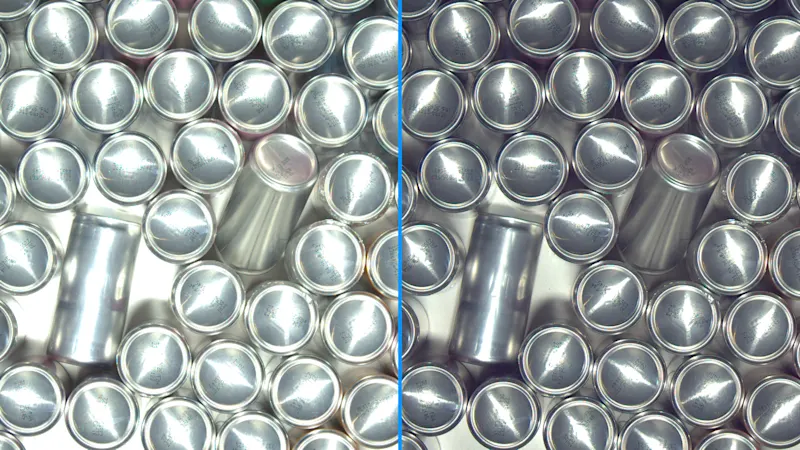
Polarization filter: Brilliant images without reflections
With polarization filters, unwanted reflections and light spots in the image can be significantly reduced. In the configuration used here, a polarization filter is placed both in front of the LED lighting and in front of the lens. This combination ensures that the reflections on the domes of the can are effectively suppressed.
The result:
Inspection features such as dents or deformations remain clearly visible and are not masked by reflections.
Fine structures and image details stand out more clearly, which noticeably improves the reliability of image evaluation and algorithm results.
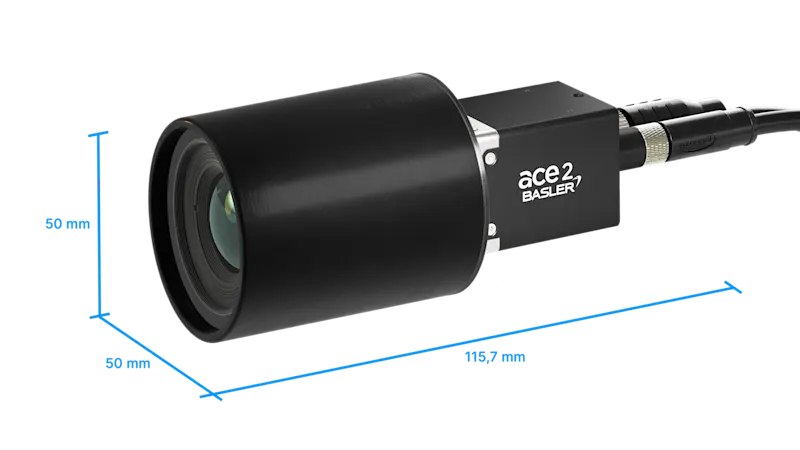
IP67 vision solution for confined installation situations
A key advantage of the ace 2 IP67 camera is its particularly compact design. In contrast to custom-made, external protective housings, which completely enclose the camera and lens and are often bulky as a result, the IP67 protection of the ace 2 is already integrated into the camera housing. This means that the camera can be easily integrated into machines even with minimal installation space.
To fully capture the 3 m wide conveyor belt, an exceptionally wide field of view is required. This requires a correspondingly large lens, resulting in dimensions of 185.9 mm × 80 mm × 80 mm (L × W × H) for the IP67 camera, lens and lens housing.
IP67 vision systems can be complex. By working closely with our customers from day one, we can avoid common pitfalls and achieve the best outcome for each individual project.
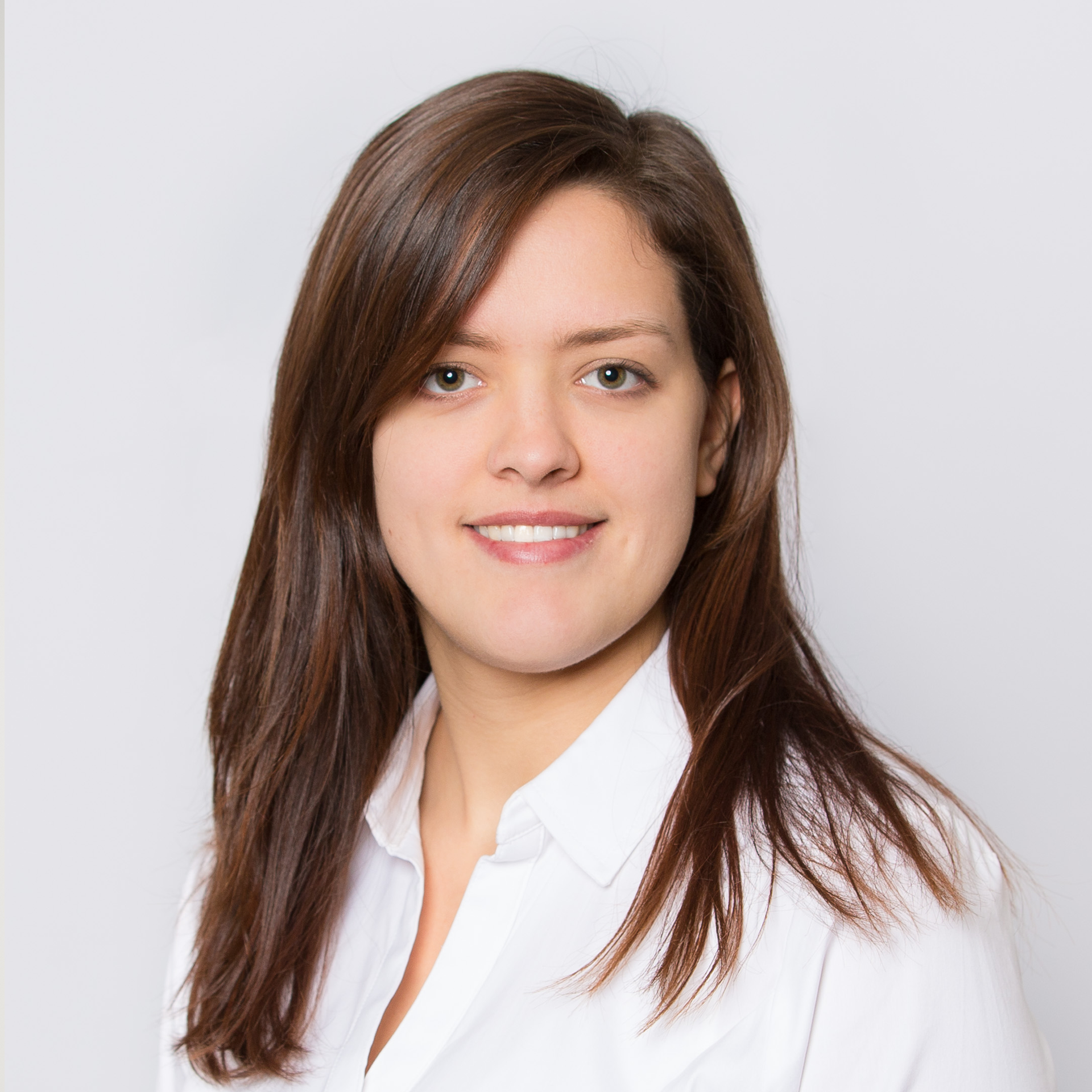
IP67 vision system for the quality control of cans
The IP67-protected vision system made from compatible components delivers reliable images under demanding environmental conditions with dust, dirt, and water.
Extracting three different types of information with AI software
The pylon AI software detects defects such as dents, identifies fallen cans, and reliably counts both total throughput and rejected units using object detection. This enables full process transparency, consistent product quality, and automated inline control.
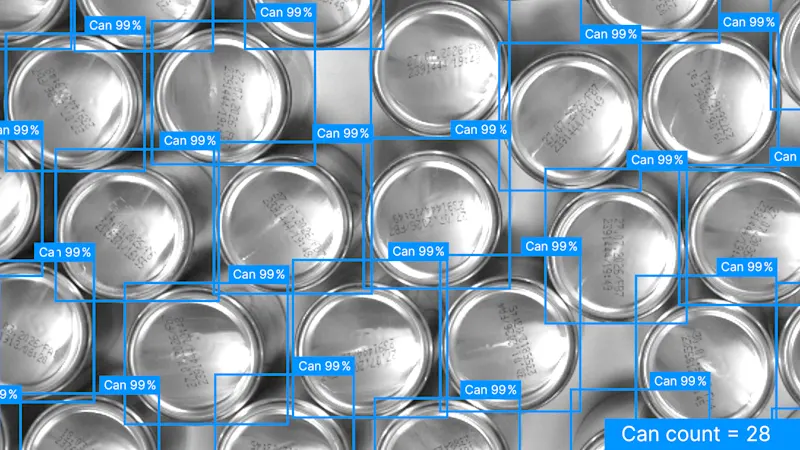
Quantity detection
For accurate batch production
The pylon AI Software recognizes and counts cans using object detection to recognize and count cans, regardless of whether they are upright or have fallen. This enables precise tracking of quantities to ensure production targets are met while avoiding overproduction or underproduction.
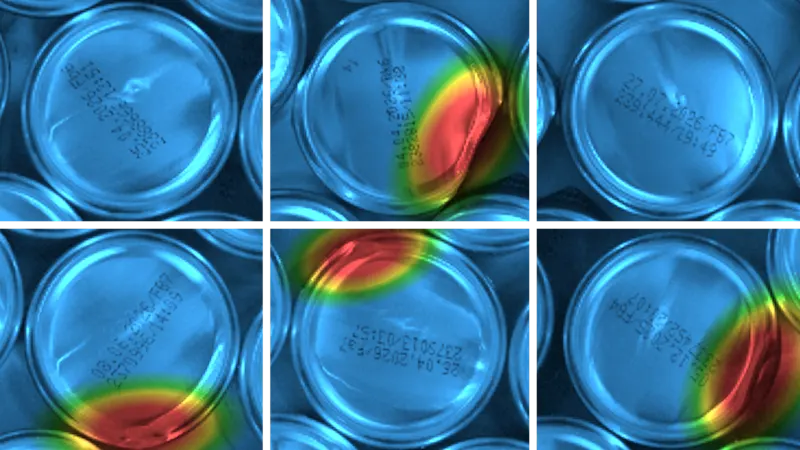
Quality assurance
No can with defects
Using the pylon AI Add-on Anomaly Detection, the software identifies damaged cans such as those with dents. These are automatically classified as "bad" and can be sorted out directly.
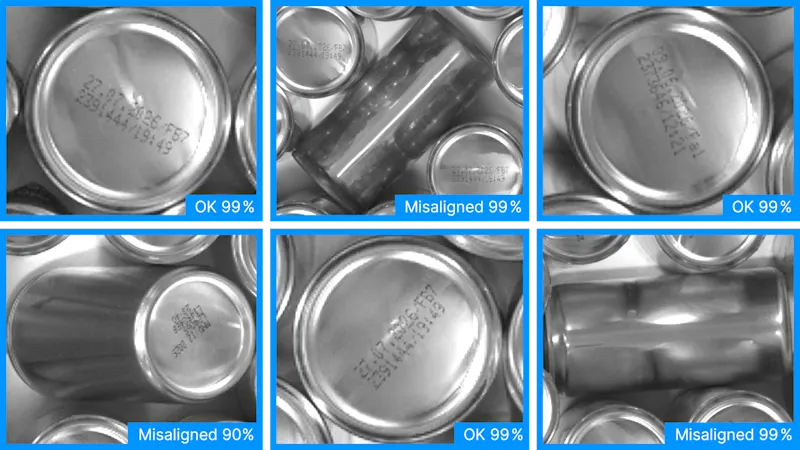
Inline process control
Recognize fallen cans
Horizontal cans are also detected and localized–the pylon AI Add-on Object Detection determines the position. The coordinates can be forwarded to robots, which can grip and erect the cans in a targeted manner.
Quality control in can production–even under demanding conditions
The IP67 vision system combined with intelligent pylon AI software provides a robust solution for inline inspection after the washing process. Even in the presence of steam, moisture, and highly reflective aluminum surfaces, the system accurately detects dents, deformations, and fallen cans. In addition, it continuously counts the cans, delivering valuable data for monitoring and optimizing the manufacturing process.
Robust IP67 components
Optimized image quality
AI-supported anomaly detection
This ensures both quality and process reliability, with a solution that is efficient and easily adaptable to individual production requirements.