Autonomous robot for production logistics
3D vision and code reading enable intelligent line feeding
- Customer
- Magazino–A Jungheinrich Company
- Location
- Munich, GER
- Date
- 2025
The fully autonomous SOTO robot automates material supply in intralogistics. Equipped with Basler 3D camera technology, it uses conveyor-integrated grippers to pick up, rotate, and place small load carriers (SLCs). Various codes mark both storage locations and the SLCs themselves.
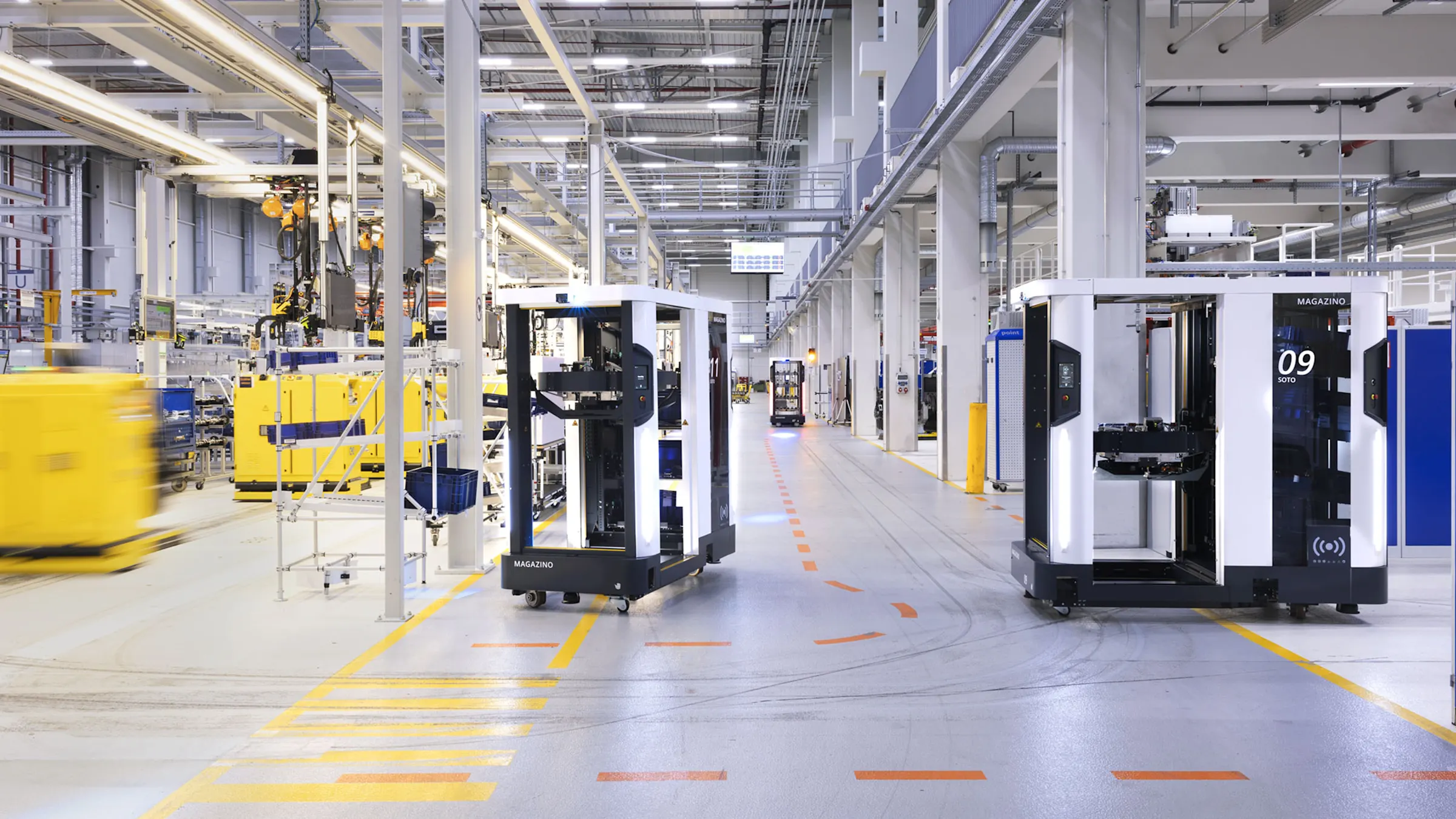
Automated material supply
Despite the high level of automation in industrial production lines, material replenishment is often still performed manually. Tugger trains and basic automated guided vehicles (AGVs) reach their limits here, as loading and unloading typically require manual intervention. The AMR SOTO provides a solution: it transports small load carriers (SLCs) fully autonomously—from the warehouse directly to the assembly line, without manual input.
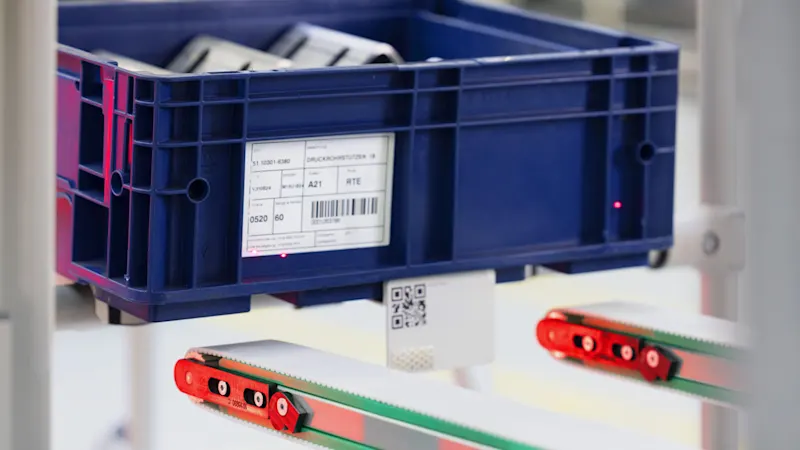
Precise handling of small load carriers
Whether at a flow rack, conveyor belt, or tugger train: SOTO transfers or picks up SLCs—for example, Euro containers—with pinpoint accuracy. It flexibly adapts to different positions and heights. A smart gripper system makes this possible: two grippers, each equipped with rotating conveyor belts, can pick up, place, and rotate SLCs. For example, SLCs can be set down on the long side and returned empties picked up again from the short side.

Independent goods picking thanks to 3D ToF control
The SOTO gripper system is guided by 3D depth data: A Basler ToF Camera is mounted at the rear of the gripper module, where it captures and measures the loading or unloading scene. Distances between 10 cm and 1.5 m are measured in real time in order to determine the coordinates of the front edge of an SLC or storage slot. Based on this data, both grippers are controlled reliably within milliseconds.
A second 3D ToF camera is integrated into the "roof" of SOTO and handles the fine-tuning of the grippers. If an SLC is detected slightly misaligned during feeding, one of the two grippers can be adjusted—moved faster or slower in real time—to correct the position. This ensures smooth, precise infeed–for reliable and efficient handling.
For precise and reliable gripper control, 3D imaging was essential—and the Basler Time-of-Flight camera was our first choice.
The Dual Exposure HDR feature has reflections reliably under control
Changing lighting conditions and reflective surfaces are common challenges in industrial environments—especially when light strikes at a shallow angle. The Basler Time-of-Flight Camera addresses this with its Dual Exposure HDR mode: two images with different exposure times are combined, allowing both highly reflective and low-reflective objects to be captured in detail. The result is a high-quality 3D point cloud—regardless of material, surface, or distance.
This makes the camera particularly suitable for dynamic production and logistics environments, where consistent image quality is essential.
Barcodes and QR codes track SLCs and identify storage slots
Barcodes and QR codes on SLCs and conveyor tables are read using 2D image processing. This enables end-to-end tracking in modern material handling systems.
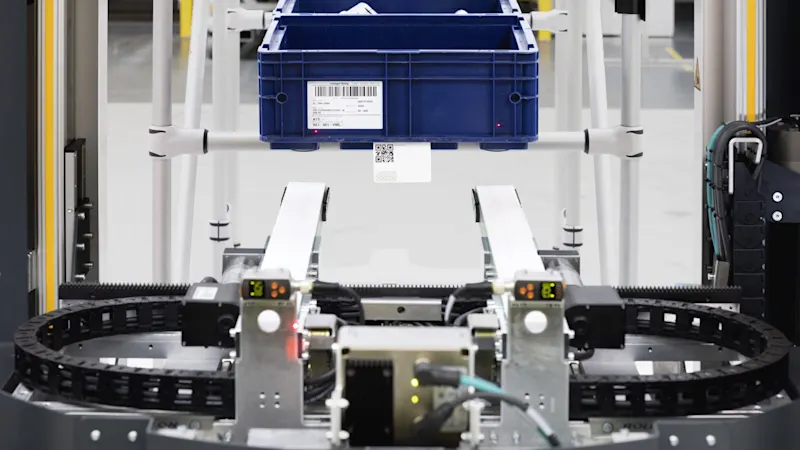
SLCs are identified and tracked using codes
Codes contain key information such as storage slot, destination, or even batch numbers. Monochrome area scan cameras capture these codes, forwarding the information to the warehouse management system. The autonomous SOTO robot is equipped with an ace 2 area scan camera, which enables the documentation of every movement of the SLCs.
Products for position control and code reading
Get this solution or a customized machine vision solution from us!
Our experts are happy to advise you on your individual vision project.
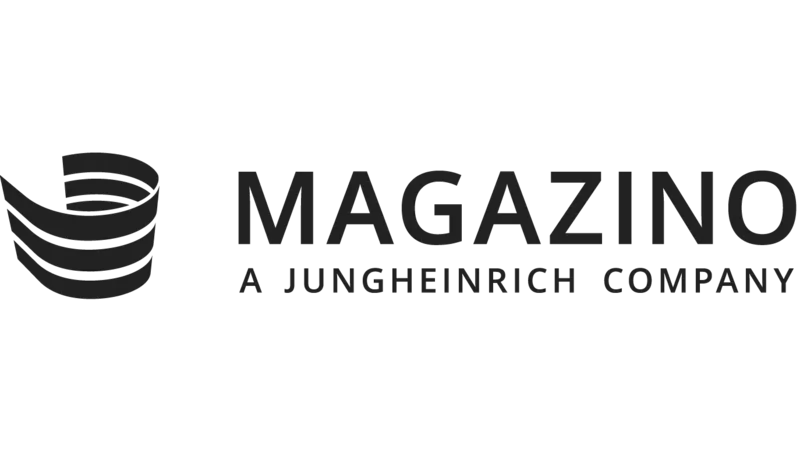
About Magazino
Magazino—a Jungheinrich company, develops and builds intelligent, mobile robots that can perceive their environment, make their own decisions and grasp objects. The autonomous robots work in parallel to humans and make processes in the areas of e‑commerce, fashion and production logistics more flexible and efficient. With 130 employees at its Munich site, Magazino is one of the largest advanced robotics teams in Europe. Magazino has been part of Jungheinrich AG since 2023.