Volume Measurement for Efficient Packing in Outbound Logistics Processes
3D cameras measure packages and fill levels of pallet cages
Packing pallet cages, pallets and other load carriers safely and efficiently is a key task in outbound logistics. Precise volume recording of parcels and goods helps to make optimum use of the available loading space and ensure smooth onward distribution. The stereo and time-of-flight camera technology measures packages precisely, detects gaps in pallet cages and thus enables optimum packing. A robot carries out all process steps autonomously.
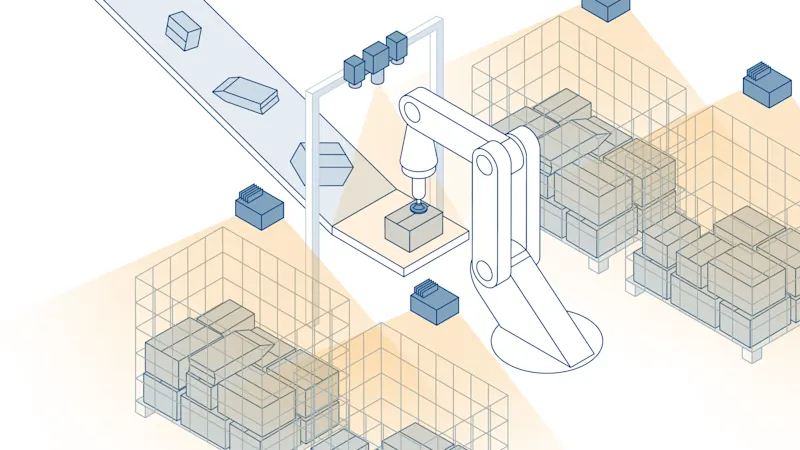
Stereo vision for maximum precision, time-of-flight technology for efficiency
The parcels, identified by their target region, are routed onto a storage surface. There they are measured and localized using stereo technology. A logistics robot picks up the parcel and a second 3D camera with ToF technology determines the appropriate place in the pallet cage intended for the respective target region. This allows the logistics robot to optimally load the pallet cage.
We have observed that a lot of manual work is still carried out in warehouse and logistics processes. Modern image processing solutions can automate sub-steps in many areas. Employees are relieved and quality checks can be carried out along process chains.
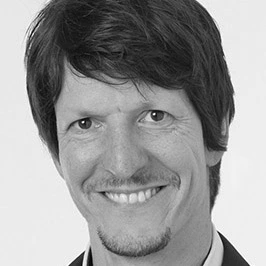
Dimensioning accurate to the millimeter thanks to Stereo Vision
With a distance of 150 cm, the 3D stereo ace camera is STA-200-547M-082616-W above the storage area. It measures the package and, in the next step, determines a suitable packing position in the pallet cage based on the dimensions.
In combination with the industrial computer that processes the 3D data, dimensioning takes less than 200 ms. This is necessary to achieve a correspondingly short processing time. We recommend providing GPU support in the computing architecture.
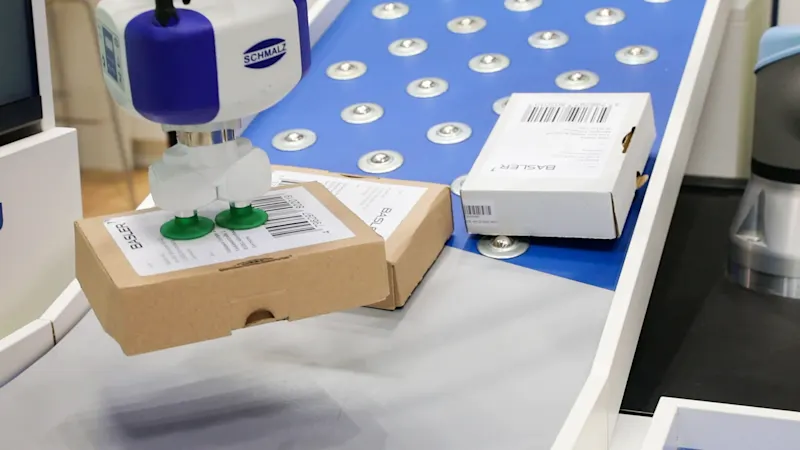
Damage-free gripping thanks to exact localization of the package surface
The 3D depth data from the stereo ace camera also provides precise positioning of the parcels. Compared to other 3D methods, the stereo vision technology enables even with varying surfaces the most precise detection of the top edge. This allows the robot's vacuum grippers to grip the parcels safely and without risk of damage.
The key to the highest precision in edge detection lies in the random dot projector, which is already integrated in the stereo ace camera: a projector projects a random pattern of dots onto the recording scene. This creates texture when little or no structure is present.
With the right 3D camera technology, robots can be controlled so that packages are handled carefully and without damage. In this way, computer vision increases accuracy, productivity and efficiency, resulting in significant cost savings in a distribution center.
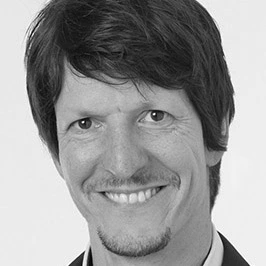
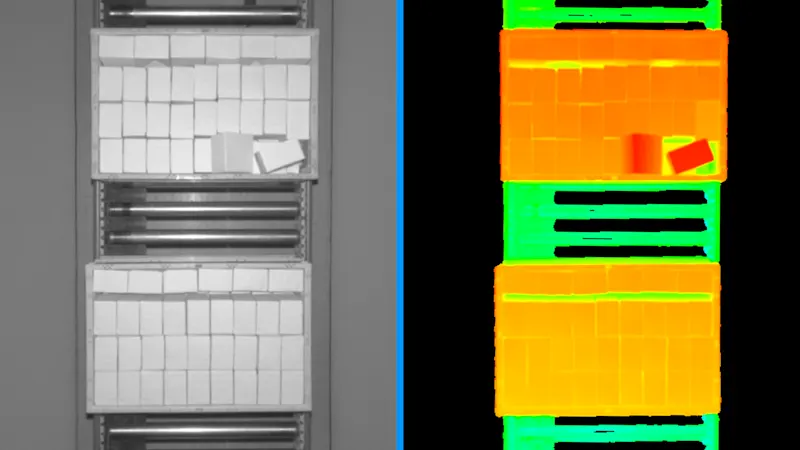
Efficient packing: Fill level detection with time-of-flight technology
3D time-of-flight cameras are installed above the parcel cages, which measure the remaining space in the cages in real time. This data is compared with the dimensions of the package just picked up and a suitable gap or the most efficient packing space possible is sought for each package. As this process step requires significantly less accuracy, the Basler ToF Camera with -102 nm a more cost-effective 3D technology can be used.
Compatible with common robot brands
Thanks to software interfaces, our vision products are compatible with a wide range of robots and gripping systems. Our robotics experts will be happy to advise you on your project.
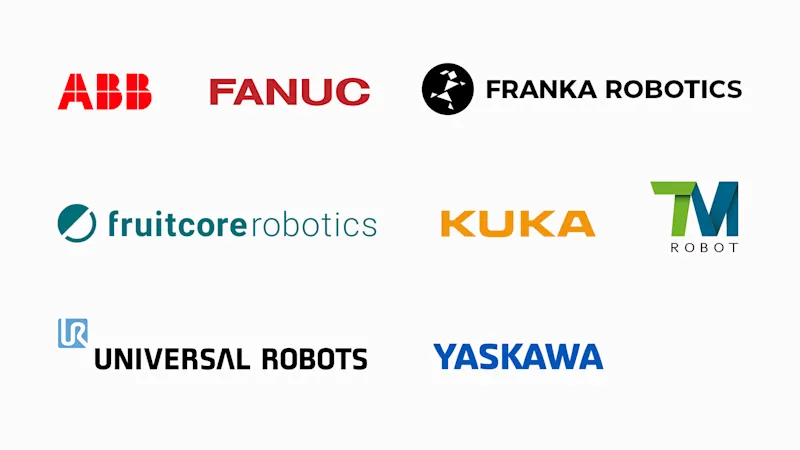