From USB to MPI CSI-2
The right interface for your embedded vision application
Choosing the right interface is crucial for the performance of your embedded vision system. The type of interface has a direct impact on the data transfer, image quality, and overall performance of your system. In this article, you will learn which interface is the right solution for your vision application.
The MIPI CSI-2 interface for embedded vision applications
The white paper provides a comprehensive insight into the relevance and features of this embedded vision interface:
What does MIPI mean?
What does MIPI CSI-2 define? What not?
What are the advantages of the MIPI CSI-2 interface?
What challenges can arise when using MIPI CSI-2?
Implementing an embedded vision system – this is what matters
Do you want to implement your vision project while controlling production costs? Then a setup with embedded vision modules offers the ideal solution.

Small and powerful – the processor board
Embedded vision systems are characterized by their small size. This allows them to be easily integrated into small devices such as drones, robots, smartphones, and cameras. The small size of the technology is achieved by a small embedded processor board that uses a System on Chip (SoC). A SoC is an electronic component that contains the core elements of a computer. Its integrated graphics unit is particularly well suited for image processing tasks.
Although a typical SoC is not as powerful as a comparable PC processor, the performance of an SoC is ideal for many applications. To ensure a cost-effective design, the SoC is soldered directly onto a small printed circuit board (PCB) that contains all the electronic components necessary for your project.
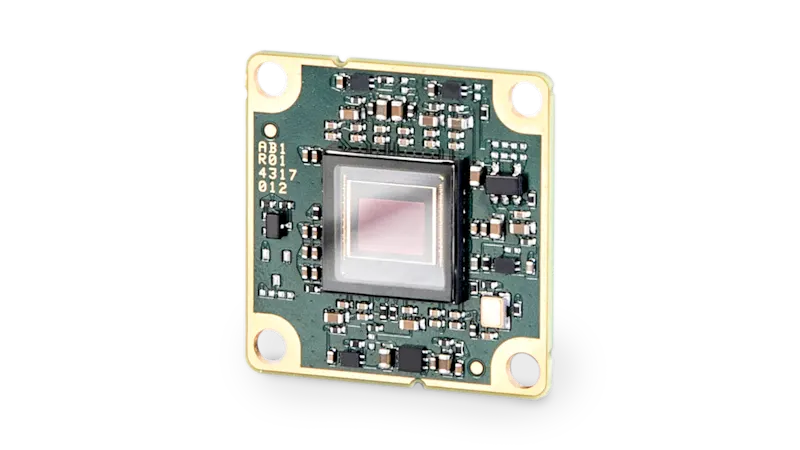
Integrating image processing – the camera module
A camera in a housing may be too big, too expensive and consume too much power for your planned solution. A good option for your vision application is a camera module – a PCB-level camera. This type of camera includes only the parts needed for your application. This saves space, and reduces electricity consumption and costs.
The camera module can be connected to the processing board via various interfaces; the most common are USB 2.0 and USB 3.0 interfaces, proprietary parallel or serial interfaces, and MIPI CSI-2 interfaces.
Selection criteria for interfaces
You should consider the following factors when deciding on an interface:
Bandwidth: The higher the bandwidth, the faster data can be collected, processed, and analyzed.
Cable length: The distances that the signal can travel without loss varies from interface to interface
Cost & availability: It is advisable to choose low-cost interfaces that are readily available from established vendors.
From USB 3.0 to MIPI CSI-2:
Common interfaces at a glance
To choose the right interface for your embedded vision application, it is helpful to compare the different options. We have summarized the advantages and disadvantages of the most common interfaces for embedded vision for you:
UBS 2.0 | UBS 3.0 | Proprietary Parallel interface | Proprietary Serial interface | MIPI CSI-2 | |
---|---|---|---|---|---|
Standardized | ✔ | ✔ | ❌ | ❌ | ✔ |
Available on SoC | Very Often | On high-end SoCs | Not very often | On FPGA SoCs | Many, typically 6 lanes available |
Bandwidth | 40 MB/s | 360MB/s | Manufacturer dependent | Manufacturer dependent | 300 MB/s/lane |
Cable length | < 5 m | < 5 m | 50 cm | Manufacturer dependent, < 3 m | < 30 cm |
Space requirements | High | High | Low | Low | Low |
Plug & play | ✔ | ✔ | ❌ | ❌ | ❌ |
Devolopment costs | Low | Low | Manufacturer dependent | Manufacturer dependent | Manufacturer dependent |
USB Interfaces
If development costs need to be tightly controlled, USB interfaces can be a good choice.
USB 2.0: is often already present on many SoCs. This means that only minimal additional hardware, such as the USB port, is needed to connect the camera to the SoC. The disadvantage of this interface is the low bandwidth of only up to 40 MB/s, which makes it impossible to operate high-resolution sensors at higher speeds.
USB 3.0: offers up to 360 MB/s, a significantly higher bandwidth than USB 2.0. Drivers and camera SDKs, for example for Linux/ARM-based embedded systems, are standardized and usually run smoothly on such systems. The plug-and-play nature of USB makes it very easy to integrate such modules into the application.
Both USB 2.0 and USB 3.0 have one thing in common: they requirerelatively large connectors and which can conflict with the strict space constraints of some applications. However, only a few high-end SoCs have USB 3.0 interfaces.
Parallel and serial interfaces
If a standardized interface is not desired, a parallel or serial interface can be the solution.
Parallel: These interfaces are usually connected to the processor board with flat flex cables. Such modules require an SoC with parallel video input , which is only available on a few SoCs. The maximum cable length is often limited to 50 cm .
Serial: Camera modules with proprietary serial interfaces are primarily intended for connection to a Field Programmable Gate Array (FPGA). If the heart of your embedded system is already an FPGA, this interface can be a good choice. These modules are also connected to the FPGA via a ribbon cable; some module manufacturers allow cable lengths of more than one meter.
The serial and parallel interfaces both require that a camera driver be available for the desired camera/SoC combination.
MIPI CSI-2 Interfaces
If bandwidth across multiple lanes is the focus of development, MIPI CSI-2 should be the first option.If bandwidth across multiple lanes is the focus of development, MIPI CSI-2 should be the first option.
MIPI CSI-2 is an interface standardized by the Mobile Industry Processor Interface Alliance (MIPI Alliance). CSI-2 is the abbreviation for "Camera Serial Interface" in the second generation. It is the most widely used interface for mobile applications and is used to connect the camera module of a smartphone to an SoC.MIPI CSI-2 is an interface standardized by the Mobile Industry Processor Interface Alliance (MIPI Alliance). CSI-2 is the abbreviation for "Camera Serial Interface" in the second generation. It is the most widely used interface for mobile applications and is used to connect the camera module of a smartphone to an SoC.
Almost all SoCs offer up to six serial lanes that can be used to connect one or more cameras. Each lane offers a bandwidth of up to 300 MB/s; so that even high-resolution camera modules can be operated at high speed. However, the cable length is limited to less than 30 cm .
It is also important here that a driver for the desired camera/SoC combination be available. Otherwise, additional development effort must be put into developing the driver and the software stack. This can be time-consuming and costly.
Conclusion: Choosing the Right Embedded Interface
Choosing the right interface depends on the conditions of your system. Decide which interface suits your system depending on bandwidth, cable length, space requirements, drivers and SoC. We offer camera modules with USB, parallel, serial or MIPI CSI-2 interfaces that are optimized for your application.