3D Robot Vision Systems for Efficient Automotive Assembly Lines
Basler vision components on robot arms are used in the 3D robot vision systems of the Chinese company Alsontech. On Volkswagen production lines, pick-and-place robots mount exhaust pipes on vehicle chassis.
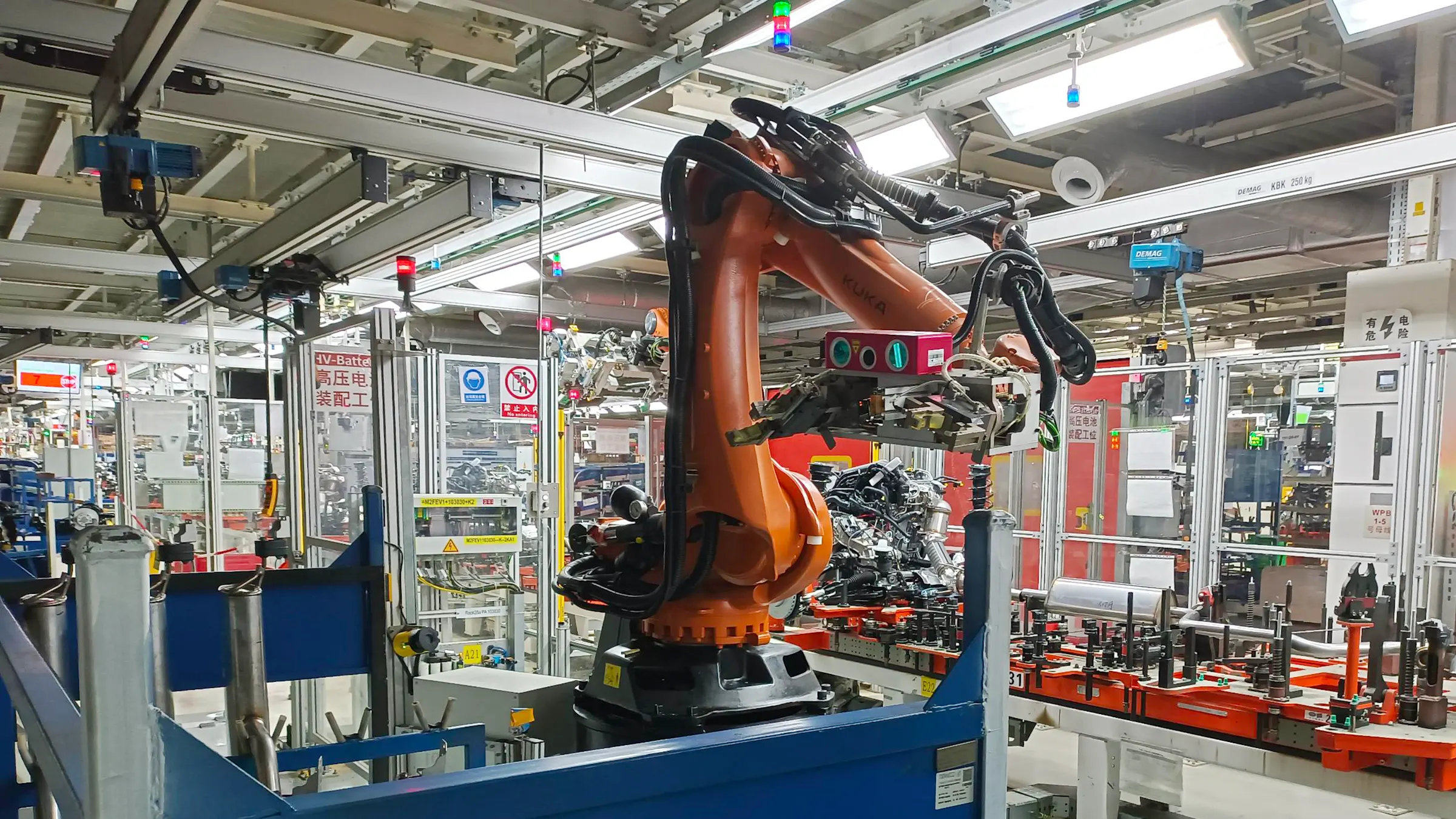
Requirements for 3D vision systems for assembly lines
The vision system must be flexible enough to recognize and work with all types of vehicle chassis and precise enough to install exhaust pipes at their exact position. Additionally, it should have a large field of view to capture the long exhaust pipes and reflective surfaces.The required accuracy for the pick-and-place robot is 99.9% and the corresponding accuracy for the 3D vision positioning system is ±1mm.
The 3D robot vision solution for automotive industry assembly lines
The vision system uses two Basler ace 2.3 MP cameras, the Alsontech laser imaging technology and a SmartVision software.
It performs three tasks:
Scanning the exhaust pipe using Basler ace industrial cameras and line-laser module
Generating a detailed cloud image with the pipe’s bend as the feature
Calculating the best unique coordinates for the robot arm to pick up an exhaust pipe and place it onto the car chassis correctly
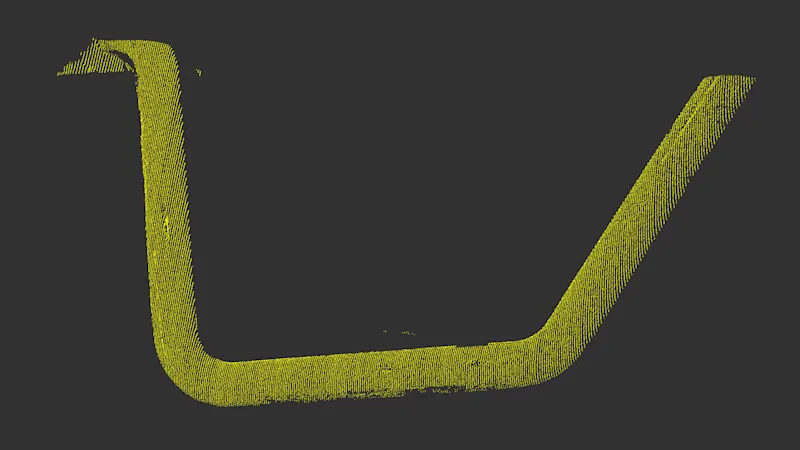
The vision system with Basler components increases the productivity of production lines by:
enabling a large field of view for the exhaust pipes, which are about 2 meters long,
providing spatial information for accurate positioning in real time,
offering great flexibility for different vehicle chassis, and
ensuring high precision to meet the daily capacity target.
Given its small footprint, the robust vision system works perfectly with the robots on Volkswagen's assembly line.
Benefits of the 3D vision solution
The main advantages of the 3D robot vision solution are:
Small footprint: the vison system is compact so that the vision-guided robot fits in the confined space of a work cell.
High accuracy: with accurate visual information to precisely navigate along its edge, the pick and place robot executes pick tasks accurately and reliably.
High flexibility: flexibility in vision system design allows the application to be extended to other car components on the same assembly line.
Reduction in overall production costs: costs decline with less workforce needed for material handling.
Easy to use software: system engineers can focus on the total automation solution.
Products for this solution
Looking to implement a comparable solution? These products will help you.