TUM Boring - Innovation in Tunnel Construction
Basler sponsors innovation project with cameras
- Customer
- TU Munich Boring Team
- Date
- April 2024
TUM Boring is an accredited student university group with over 60 members who want to work together to shape the mobility of the future and change it for the better. With the help of sponsors including Basler cameras, the team took part in Elon Musk's "Not-a-Boring Competition", in which the aim is to bore a 30 m long and 50 cm wide tunnel as quickly and precisely as possible to simulate creating the infrastructure for future forms of mobility.
TUM Boring - Innovation in Tunneling is a student initiative based in Munich that has set itself the goal of building the fastest tunnel boring machine. With a team of around 60 dedicated students, they have won Elon Musk's prestigious "Not-a-Boring Competition" in both 2021 and 2023 due to remarkable advances in tunneling technology.
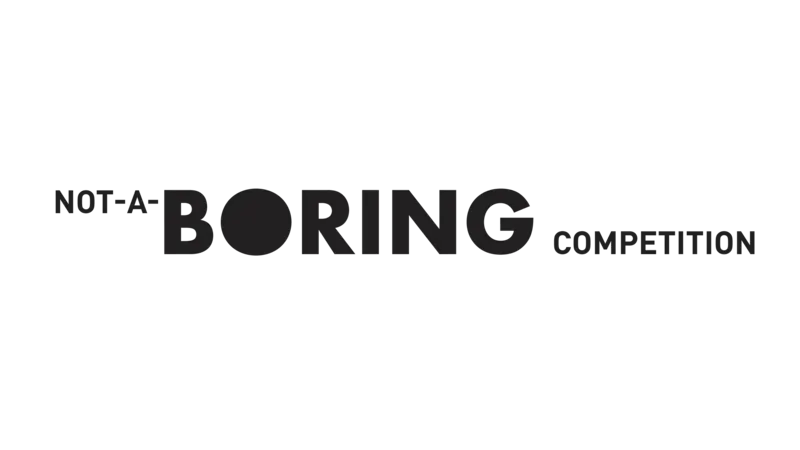
The competition - innovation in tunnel construction
Driven by the desire to change the current status quo of tunnel boring technology, Elon Musk's "The Boring Company" has been running the "Not-a-Boring Competition" since July 2020. They challenged students from all over the world to design and build a machine that bores tunnels faster than a snail can crawl: 100 meters in 24 hours. Until now, tunnel boring machines have only managed around 40 meters per day. The aim of the competitions is to drill a tunnel with a diameter of 50 cm and a length of 30 meters as quickly and precisely as possible at a depth of 1.5 meters.
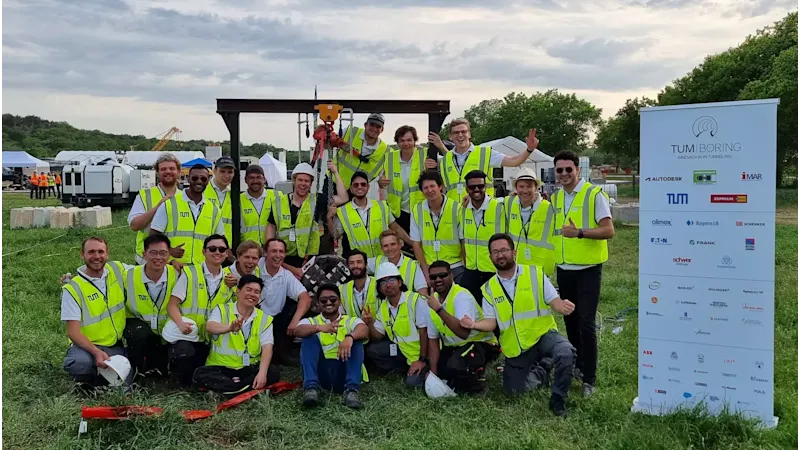
TUM Boring Team - together to victory
The TUM Boring - Innovation in Tunneling team is a rotating team consisting of 60 members. Most of them are students, from over 16 faculties and from 16 different countries around the world. This diversity of the team is one of its strengths. Prospective mechanical engineers , engineers, computer scientists, humanities scholars, social scientists, and economists work together in an interdisciplinary approach.
Each competition (2021 and 2023) takes around 14 months of project work to develop their tunnel construction innovations.
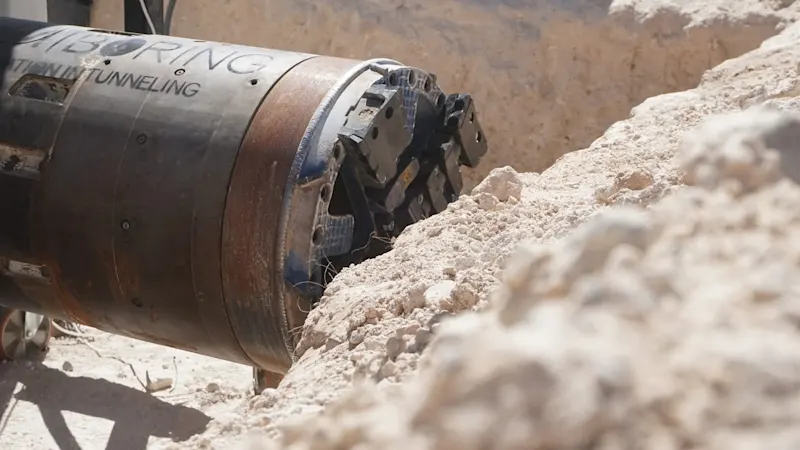
Drilling technology - the key to success
2021
Dry material removal concept for very high removal rates and easy material disposal
Innovative bearing for the tunnel segments, resulting in faster progress and less setup logistics
2023
Horizontal start directly from the surface, so no start shaft is required
Drilling of tight curve radii through the use of flexible pipes.
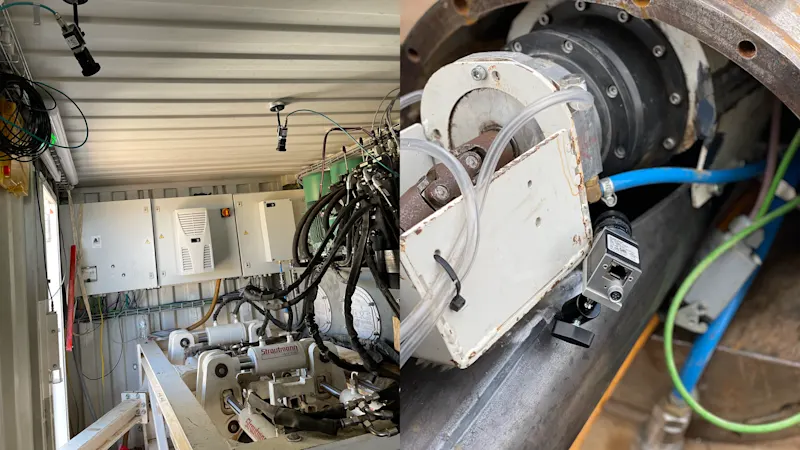
The role of Basler - flawless inspection
The Basler cameras were commissioned and configured using the pylon Software Suite. Several Basler ace 2 cameras were mounted in the drilling machine to monitor precision. The cameras in the cutting head capture the material removal and show the removal process.
Additional area scan cameras installed in the container enable safety and control. A live image was transmitted to the pylon Viewer to ensure that functional sequences are carried out correctly. The presence of people in the container was also checked before the machine was started, to meet the highest safety standards.
Interested in what's next for TUM Boring?
We wish the TUM Boring Team all the best for further iterations of tunnel boring and for upcoming competitions and we're keeping our fingers crossed!
Want to stay up-to-date and not miss anything? Check out their website , or follow the Instagram or LinkedIn channel.