Positionnement précis : assurance qualité pour l’empilage
Lors de l’assemblage des cellules de batterie à poche, le processus d’empilage nécessite une superposition précise de feuilles d’électrodes individuelles et un séparateur. La vision industrielle fournit un positionnement précis dans la plage du μm, assurant un empilage précis qui est essentiel pour la qualité et la durée de vie de la cellule de batterie résultante.
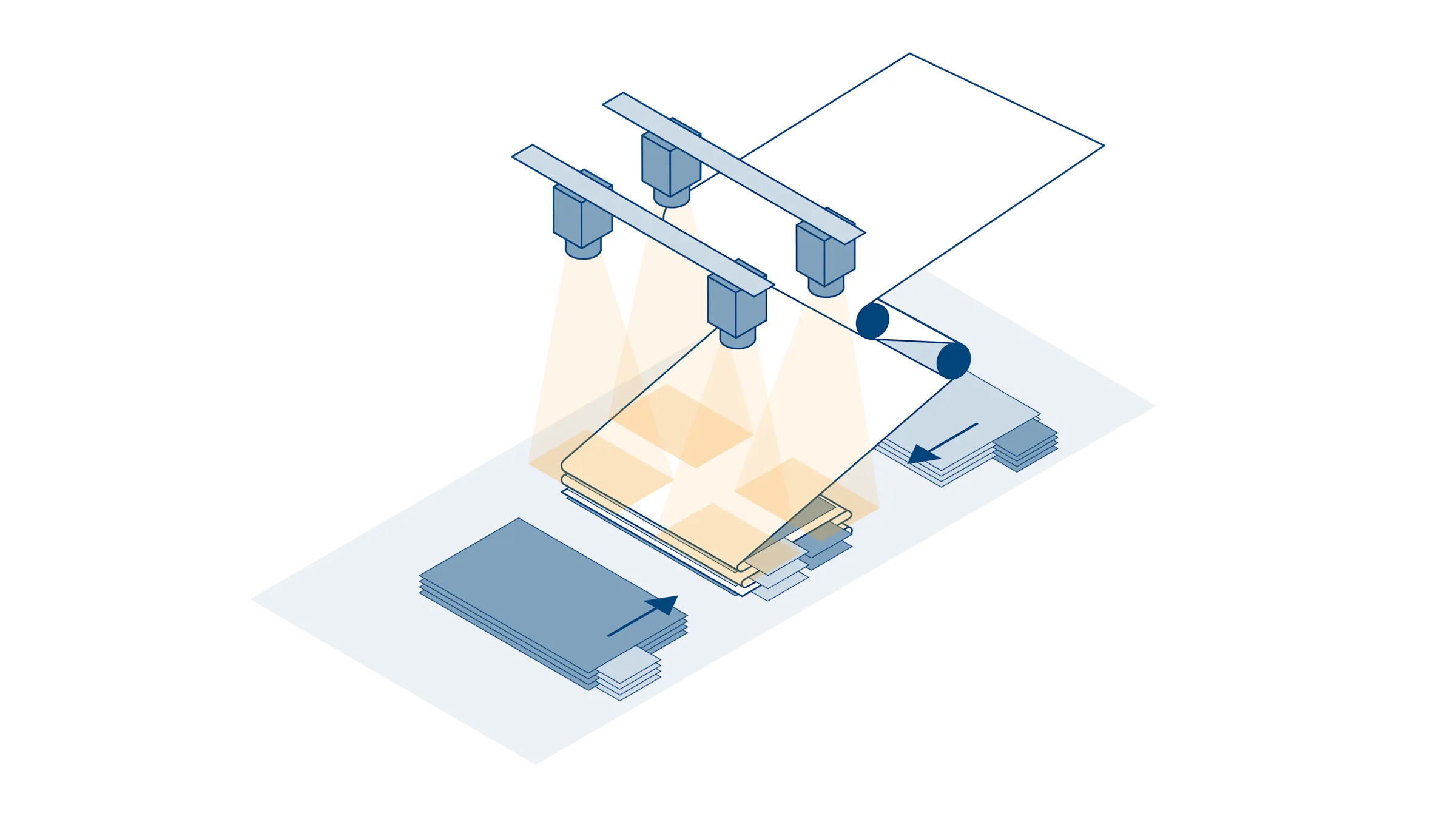
Pliage en Z dans l’assemblage de la cellule de poche
Les batteries à poche sont fabriquées en empilant des feuilles de cellules recouvertes d’électrodes. Dans le processus de pliage en Z, les feuilles d’anode et de cathode prédécoupées sont insérées dans la feuille de séparation des deux côtés. La feuille de séparation est fournie sous la forme d’un matériau enroulé à bande continue. Cette disposition en forme de Z des feuilles d’électrodes et de la feuille de séparation donne son nom au processus.
Le processus est répété en continu et il est possible de créer jusqu’à 120 couches. Une fois terminé, le fabricant de la batterie scelle les bords de la feuille. Ensuite, la pile de cellules est enveloppée dans du papier d’aluminium, le papier d’aluminium est coupé et le reste est fixé avec du ruban adhésif.
Précision au micron dans le positionnement des plaques d’électrodes
Les systèmes de préhension à vide prélèvent des feuilles d’anode et de cathode individuelles et les placent alternativement sur le séparateur. Le positionnement précis des feuilles d’électrodes et du séparateur est essentiel à la qualité de cette étape du processus.
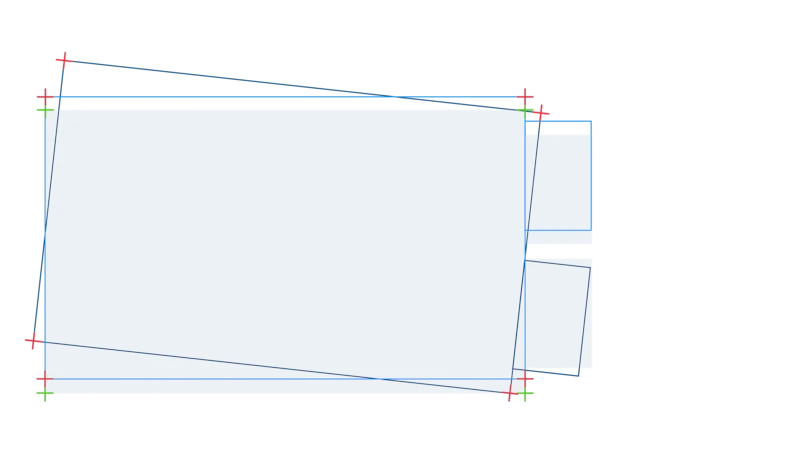
L' alignement des bords doit être aussi précis que possible, avec des tolérances de l’ordre du μm : Des écarts inférieurs à 200 μm sont acceptables. Des vitesses élevées ajoutent au défi de cette étape du processus : les feuilles d’électrodes sont ramassées et placées sur l’empilement de cellules en moins d'1 seconde !
La vision industrielle fournit le contrôle de qualité nécessaire
La production de cellules de batterie est soumise à des réglementations strictes afin d’éliminer les dangers potentiels qui pourraient résulter d’erreurs dans les différentes étapes de production. Les systèmes de vision industrielle, composés de caméras et de logiciels haute performance, garantissent que les pièces finies sont produites correctement.
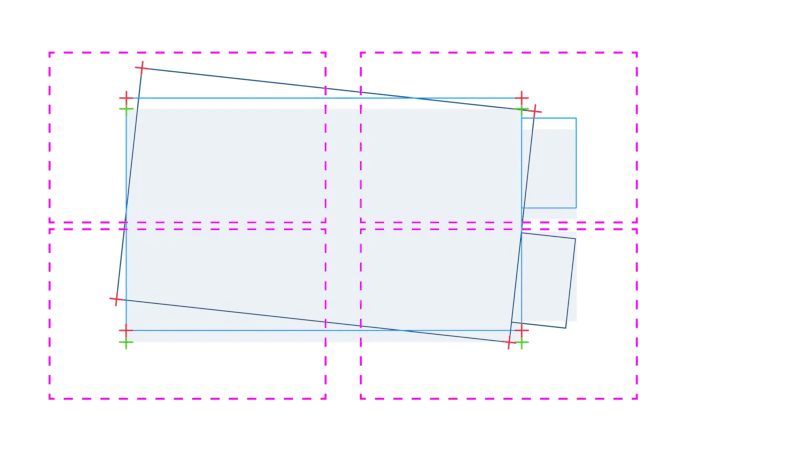
Quatre caméras synchronisées
Dans le processus d’inspection, quatre caméras vérifient le bon positionnement des feuilles d’électrodes à chaque coin. La norme CoaXPress 2.0 assure un déclenchement précis dans les systèmes multi-caméras et la transmission de données en temps réel. Les données d’image capturées peuvent être analysées à l’aide du logiciel pylon vTools afin de déterminer l’empilement exact des feuilles d’électrodes.
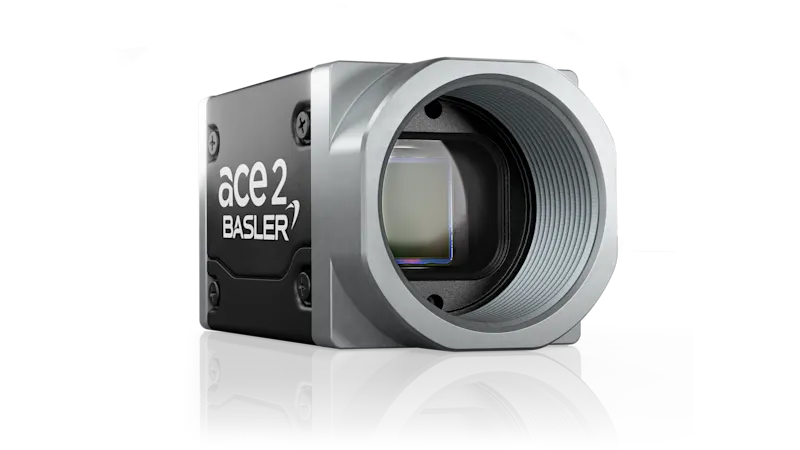
Hautes performances dans un petit facteur de forme : caméra ace 2 V
Encombrement peu encombrant de 29 mm x 29 mm pour une intégration facile de la caméra ace 2 V dans les systèmes d’empilage existants et nouveaux
Des images brillantes et haute résolution grâce aux capteurs Sony Pregius S et aux fonctionnalités du firmware Basler
L’interface CXP-12 permet des bandes passantes allant jusqu’à 12,5 Gbit/s
Solution à câble unique via Power over CoaXPress pour un câblage et une intégration faciles
Mesures d’écart robustes et fiables avec le logiciel pylon vTools
Le logiciel pylon vTools analyse les images capturées. Par exemple, une recette en plusieurs étapes peut être créée comme suit :
vTool Calibration & Rectification: Assurez-vous que les distances mesurées sont affichées en métriques calibrées. Compensez les distorsions radiales et de perspective causées par les paramètres de la caméra.
vTool Measurements: Une image de modèle peut être utilisée pour définir un rectangle de mesure. Au cours de l’étape du processus, d’éventuels écarts par rapport à d’autres images acquises de feuilles d’anode et de cathode empilées sont générés :
dans les coordonnées, s’il y a une rotation
ou dans les métriques pour les distances pour cibler les arêtes.
Prétraitement d’images pour la gestion de données d’images volumineuses
Gestion allégée des données : grâce à l’interface CXP-12, le système peut être étendu avec un prétraitement d’image basé sur la carte d’acquisition d’images. Cela permet d’analyser de grandes quantités de données d’image de manière ciblée, réduisant ainsi la charge sur le processeur de l’ordinateur'
Notre logiciel VisualApplets est le complément parfait de la dernière génération de cartes d’acquisition d’images imaFlex programmables.
Produits pour cette solution
Vous cherchez à mettre en œuvre une solution comparable ? Ces produits vous aideront.