Le rôle de la vision par ordinateur dans l’industrie 4.0
Des mots à la mode tels que l’industrie 4.0, l’Internet des objets (IoT), l’usine intelligente, le Big Data, le jumeau numérique et l’intelligence artificielle décrivent l’automatisation croissante des installations de production et la mise en réseau d’une grande variété de systèmes. L’objectif : intégrer le plus complètement possible les technologies de l’information et donc la vision par ordinateur dans les processus industriels.
Systèmes de vision pour l’industrie 4.0
Notre livre blanc décrit la configuration de l’usine intelligente de l’industrie 4.0 par rapport à la configuration d’usine classique d’aujourd’hui. Cela révèle un certain nombre d’avantages de la configuration intelligente en raison des nouvelles technologies et des exigences pour le système de vision du futur.
Les systèmes de vision en tant que contrôleurs de processus et fournisseurs de données infatigables
La mise en réseau des données de la caméra avec les données de production et leur analyse optimisent la production. Les écarts tels que les goulets d’étranglement, les inefficacités et le comportement incorrect des équipements peuvent ainsi être détectés automatiquement à un stade précoce et corrigés en temps réel : par exemple, la modification des paramètres de processus ou la commande de matériaux d’usure.
Des technologies intelligentes pour l’efficacité et la sécurité
Les applications possibles des systèmes de vision intelligente sont multiples. Six domaines d’application clés montrent comment ces technologies sont appliquées dans la pratique et quels avantages elles offrent :
Produits de vision pour les usines en réseau
Parmi les capteurs les plus importants et les plus puissants dans un environnement d’usine automatisée figurent les systèmes de vision avec caméras. Ils contribuent à numériser les processus de production, à augmenter la flexibilité et à relever avec succès les défis de l’industrie 4.0.
Comment la mise en réseau des données rendra l’usine de demain intelligente
Le terme usine intelligente décrit la mise en réseau intelligente dans le domaine de l’automatisation industrielle. La connaissance, composée de données et de processus, est une condition préalable fondamentale à une usine intelligente. D’où vient cette connaissance ?
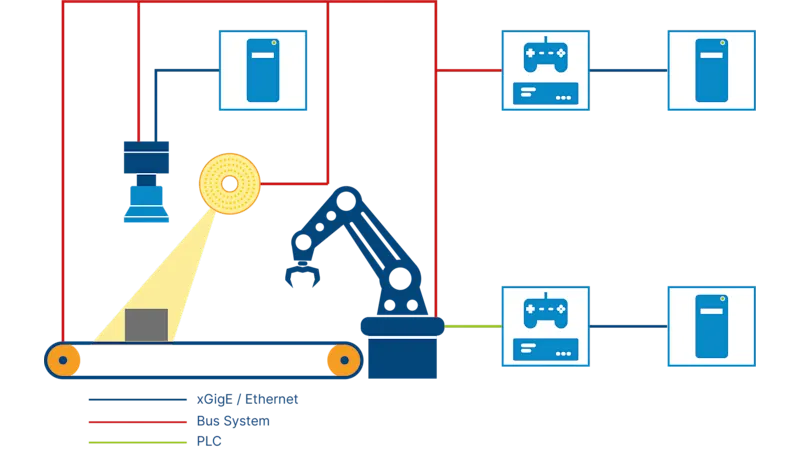
Classic factory setup with field bus systems
Data is usually collected using sensors, which also include imaging devices such as cameras. However, without appropriate processing, the data from the sensors is worthless. It must be made usable for several systems and components so that it can serve as a basis for decisions in processes. This is exactly where the factory becomes smart.
The secret lies in networking all individual and sub-systems involved. The basis of their networking is usually a so-called field bus system, which connects all sensors and actuators via the same data lines—both with each other and with an automation device, for example a control system (PLC).
Inconvénients des systèmes de bus de terrain dans l’automatisation industrielle moderne
Dans les usines modernes, les sous-systèmes et les appareils sont souvent placés loin les uns des autres. Par conséquent, les systèmes de bus Ethernet en temps réel sont souvent utilisés, car la norme Ethernet est largement utilisée, fournit du matériel peu coûteux tel que des câbles et des commutateurs, et permet de longues longueurs de câble entre les systèmes. Cependant, ces systèmes présentent des inconvénients :
Paysagesde systèmes propriétaires: De nombreuses solutions Ethernet en temps réel sont spécifiques à un fournisseur, ce qui rend difficile l’interopérabilité entre différents appareils et systèmes.
Descriptibilité: les possibilités de décrire les fonctions des composants et des sous-systèmes de manière claire et standardisée sont souvent limitées. Il est donc difficile d’intégrer et de maintenir des systèmes complexes.
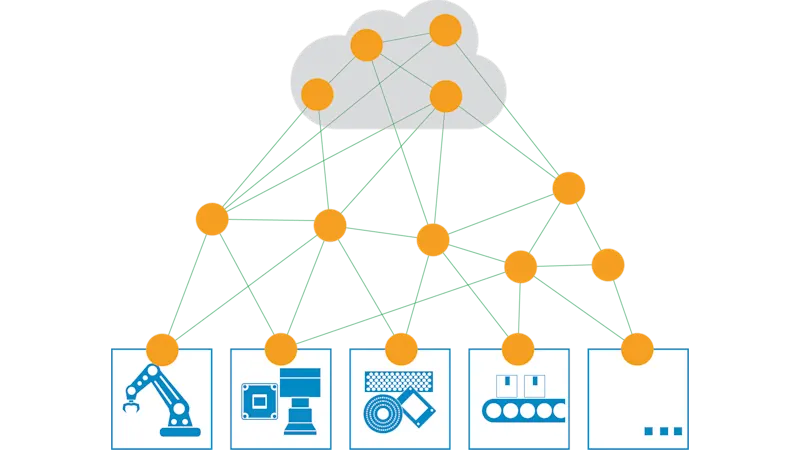
Mise en réseau grâce à umati et à la norme OPC UA
Comme tous les autres sous-systèmes, le système de vision doit être connecté à tous les autres systèmes et au système de contrôle central, tant en termes de matériel que de logiciel. Cela se fait au moyen de normes d’échange de données spéciales pour la communication. Ces normes donnent aux différents sous-systèmes un langage machine commun, pour ainsi dire, afin d’assurer une interopérabilité facile. L’une de ces normes est umati (Universal Machine Technology Interface). Il utilise OPC UA comme norme d’interface ouverte et universelle.
OPC UA rend les données de la machine lisibles par machine et sémantiquement descriptibles. La norme assure le traitement, par exemple, des données de capteurs et des commandes de commande, elle spécifie leur transport et détermine les interfaces entre les systèmes et les mécanismes de sécurité. Avec l’aide d’OPC UA, les différents composants d’un niveau peuvent être mis en réseau horizontalement et verticalement entre les différents niveaux.
Dans l’industrie 4.0, les technologies de pointe devraient conduire à des augmentations significatives de l’efficacité. Pour que la technologie complexe de la production reste facile à contrôler, les normes et la sécurité dans l’interaction de tous les composants du système sont importantes. OPC UA offre les deux : des protocoles machine-to-machine simples et sécurisés régulent la communication et rendent utilisables les avantages de l’industrie 4.0.
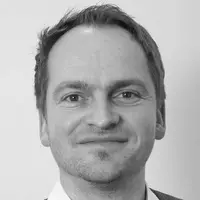

Capacité en temps réel dans l’usine en réseau
La norme OPC UA peut être utilisée à tous les niveaux de la configuration d’une usine : du niveau le plus bas du terrain, où se trouvent les capteurs et les actionneurs, aux couches d’information abstraites telles que SCADA (Supervisory Control and Data Acquisition), ERP (Enterprise Resource Planning) ou le cloud.
Indispensable pour une utilisation efficace dans tous les domaines d’une usine intelligente est en temps réel. À cette fin, la norme offre des options d’extension telles que la mise en réseau sensible au temps (TSN). TSN vise à assurer la transmission de données sur des réseaux Ethernet avec une très faible latence et une haute disponibilité. OPC UA TSN est également une condition préalable au transfert d’images directement du système de vision via OPC UA vers les autres sous-systèmes ou l’unité de contrôle.
OPC UA modifie la configuration d’usine classique
OPC UA peut être utilisé pour sauvegarder des composants matériels (PC, contrôleurs) et des logiciels incohérents, parfois incompatibles. En conséquence, les paysages de systèmes propriétaires de divers sous-systèmes sont fusionnés dans des configurations hautement intégrées et allégées . Un API ou un autre hôte fait office d’interface centrale des systèmes, qui contient désormais tous les sous-systèmes ou leurs logiciels. Ce nœud central est à son tour l’interface avec les systèmes de niveau supérieur tels que les systèmes ERP.
Dans une telle configuration, il serait possible de connecter facilement à la fois la bande transporteuse et le robot ainsi que les différents composants du système de vision à l’aide de voies de transmission standardisées. Avec leur PTP (Precision Time Protocol), les caméras fournissent déjà la base d’une capacité en temps réel lorsque OPC UA est utilisé en standard et que d’éventuelles extensions telles que TSN sont disponibles.